Self-leveling floor mortar and preparation method thereof
A mortar and leveling technology, which is applied in the field of self-leveling floor mortar and its preparation, can solve the problems of reducing laying efficiency and long drying and curing time of self-leveling floor mortar
- Summary
- Abstract
- Description
- Claims
- Application Information
AI Technical Summary
Problems solved by technology
Method used
Image
Examples
Embodiment 1
[0048] A self-leveling floor mortar, which is composed of the following raw materials by weight: Portland cement 16-25 parts, aluminate cement 12-15 parts, quartz sand 40-50 parts, defoamer 2-5 parts, gypsum 5-10 parts parts, 5-10 parts of emulsion, 6-10 parts of deionized water, 1-2 parts of quick-drying curing agent; among them, 15-20 parts of stearic acid in quick-drying curing agent, 5-10 parts of sodium tripolyphosphate, poly 4-6 parts of formaldehyde, 10-12 parts of vinyl acetate.
[0049] Each raw material is produced according to the preparation process, and a 2m*2m foundation is selected for laying, and the curing time of the self-leveling floor mortar is inspected.
Embodiment 2
[0051] A self-leveling floor mortar, which is composed of the following raw materials by weight: Portland cement 16-25 parts, aluminate cement 12-15 parts, quartz sand 40-50 parts, defoamer 2-5 parts, gypsum 5-10 parts 5-10 parts of emulsion, 6-10 parts of deionized water, 2-3 parts of quick-drying curing agent; among them, 15-20 parts of stearic acid in quick-drying curing agent, 5-10 parts of sodium tripolyphosphate, poly 4-6 parts of formaldehyde, 10-12 parts of vinyl acetate.
[0052] Each raw material is produced according to the preparation process, and a 2m*2m foundation is selected for laying, and the curing time of the self-leveling floor mortar is inspected.
Embodiment 3
[0054] A self-leveling floor mortar, which is composed of the following raw materials by weight: Portland cement 16-25 parts, aluminate cement 12-15 parts, quartz sand 40-50 parts, defoamer 2-5 parts, gypsum 5-10 parts parts, 5-10 parts of emulsion, 6-10 parts of deionized water, 3-4 parts of quick-drying curing agent; among them, 15-20 parts of stearic acid in quick-drying curing agent, 5-10 parts of sodium tripolyphosphate, poly 4-6 parts of formaldehyde, 10-12 parts of vinyl acetate.
[0055] Each raw material is produced according to the preparation process, and a 2m*2m foundation is selected for laying, and the curing time of the self-leveling floor mortar is inspected.
[0056] The use effect of the obtained self-leveling floor mortar is shown in Table 1.
[0057] Drying time of self-leveling mortar Example 1 6h Example 2 5h Example 3 4.5h
[0058] Table 1
[0059] It can be seen from Examples 1-3 that with the increase of the quick-d...
PUM
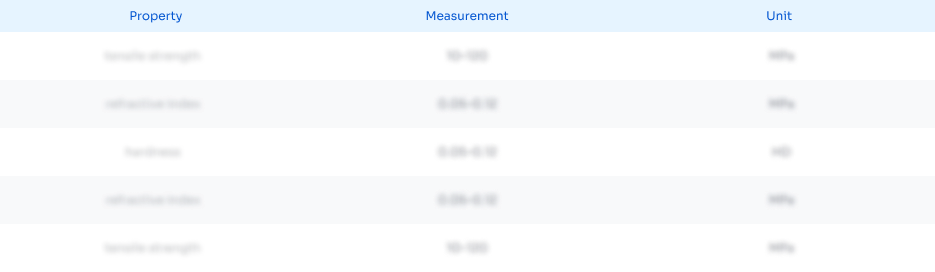
Abstract
Description
Claims
Application Information

- R&D
- Intellectual Property
- Life Sciences
- Materials
- Tech Scout
- Unparalleled Data Quality
- Higher Quality Content
- 60% Fewer Hallucinations
Browse by: Latest US Patents, China's latest patents, Technical Efficacy Thesaurus, Application Domain, Technology Topic, Popular Technical Reports.
© 2025 PatSnap. All rights reserved.Legal|Privacy policy|Modern Slavery Act Transparency Statement|Sitemap|About US| Contact US: help@patsnap.com