Textile fabric processing device with heat insulation function and dyeing production method thereof
A processing device and technology for textile fabrics, applied in the direction of cleaning devices for processing textile materials, accessories for textile processing machines, equipment configuration for processing textile materials, etc., can solve the problems of single printing patterns, low cost, color errors, etc., and achieve increased contact area, avoiding the breakage of rotating blades, and reducing the effect of pressure
- Summary
- Abstract
- Description
- Claims
- Application Information
AI Technical Summary
Problems solved by technology
Method used
Image
Examples
Embodiment Construction
[0031] The technical parties in the embodiments of the present invention will be clearly and completely described below in conjunction with the accompanying drawings in the embodiments of the present invention. Obviously, the described embodiments are only some, not all, embodiments of the present invention. Based on the embodiments of the present invention, all other embodiments obtained by persons of ordinary skill in the art without making creative efforts belong to the protection scope of the present invention.
[0032] see Figure 1-9 , an embodiment provided by the present invention: a textile fabric processing device with heat insulation, including a dyeing device 1, the inside of the dyeing device 1 is movably connected with a rotary rod 2, and the left end of the rotary rod 2 is fixedly connected with a first motor 3 The bottom of the first engine 3 is movably connected with a support frame 4, the bottom of the support frame 4 is fixedly connected with a mounting plat...
PUM
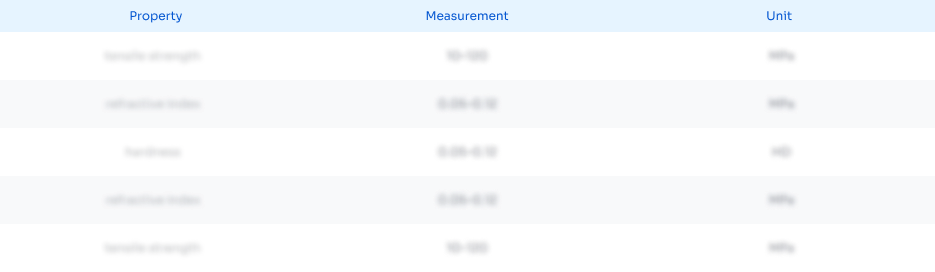
Abstract
Description
Claims
Application Information

- R&D
- Intellectual Property
- Life Sciences
- Materials
- Tech Scout
- Unparalleled Data Quality
- Higher Quality Content
- 60% Fewer Hallucinations
Browse by: Latest US Patents, China's latest patents, Technical Efficacy Thesaurus, Application Domain, Technology Topic, Popular Technical Reports.
© 2025 PatSnap. All rights reserved.Legal|Privacy policy|Modern Slavery Act Transparency Statement|Sitemap|About US| Contact US: help@patsnap.com