Temperature-resistant thick oil viscosity-reducing polymer as well as preparation method and application thereof
A technology of polymer and polymer solution, applied in the direction of drilling composition, chemical instruments and methods, etc., can solve the problems of poor affinity and temperature resistance of heavy oil viscosity reducer
- Summary
- Abstract
- Description
- Claims
- Application Information
AI Technical Summary
Problems solved by technology
Method used
Image
Examples
preparation example Construction
[0046] In yet another specific embodiment of the present invention, a method for preparing the above-mentioned temperature-resistant heavy oil viscosity-reducing polymer is provided, including:
[0047] (1) Under an inert atmosphere, sequentially add acrylamide monomer, sodium acrylate monomer, hydrophobic monomer, and temperature-resistant functional monomer into water, and stir until clear to obtain solution I;
[0048] (2) Continue to add micro-crosslinking monomer and temperature stabilizer to solution I, stir until all dissolve to obtain solution II;
[0049] (3) Add the initiator into the solution II after heating up, stir, stop stirring when the solution becomes viscous, remove the inert atmosphere, and seal the reaction.
[0050] In yet another specific embodiment of the present invention, in step (1), the inert atmosphere is nitrogen;
[0051] In yet another specific embodiment of the present invention, in step (3), the heating temperature is controlled to be 50-70°C...
no. 1 example
[0059] A method for preparing a temperature-resistant heavy oil viscosity-reducing polymer, comprising the steps of:
[0060] (1) Raw materials: acrylamide 5.544g; sodium acrylate monomer 1.368g; hydrophobic monomer 0.465g; temperature-resistant functional monomer 0.311g; initiator 0.0023g; micro-crosslinking monomer 0.0384g; temperature stabilizer 0.0154g; Distilled water 23.064g.
[0061] Wherein: the hydrophobic monomer is selected from cetyl dimethyl allyl ammonium chloride; the temperature-resistant functional monomer is selected from 2-acrylamide-2-methylpropanesulfonic acid; the initiator is selected from azobisisobutylamidine hydrochloride; micro-crosslinking monomer selection of triallyl urate; temperature stabilizer selection of sodium thiosulfate.
[0062] (2) Weigh acrylamide, sodium acrylate, hexadecyldimethylallyl ammonium chloride, 2-acrylamide-2-methylpropanesulfonic acid respectively according to the above-mentioned content, under the condition of feeding nit...
no. 2 example
[0065] A kind of preparation method of common amphiphilic polymer, comprises steps:
[0066] (1) Raw materials: acrylamide 5.57978g; sodium acrylate monomer 1.44g; hydrophobic monomer 0.465g; initiator 0.0022g; deionized water 22.4543g.
[0067] Wherein: the hydrophobic monomer is selected from cetyl dimethyl allyl ammonium chloride; the initiator is selected from azobisisobutylamidine hydrochloride.
[0068] (2) Weigh acrylamide, sodium acrylate, and cetyldimethylallyl ammonium chloride respectively according to the above contents, and under the condition of feeding nitrogen, successively mix acrylamide, sodium acrylate, cetyldimethylammonium Allyl ammonium chloride was added to water and stirred at high speed until the solution became clear.
[0069] (3) Raise the temperature to 55°C, add the initiator azobisisobutylamidine hydrochloride into the solution in (2), keep stirring at a high speed, stop stirring when the solution becomes viscous, remove the nitrogen gas, seal an...
PUM
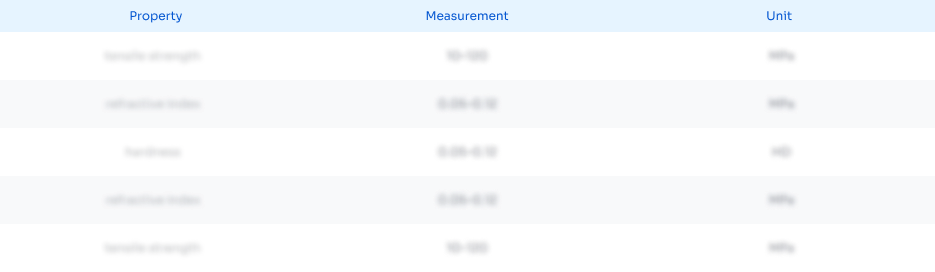
Abstract
Description
Claims
Application Information

- R&D Engineer
- R&D Manager
- IP Professional
- Industry Leading Data Capabilities
- Powerful AI technology
- Patent DNA Extraction
Browse by: Latest US Patents, China's latest patents, Technical Efficacy Thesaurus, Application Domain, Technology Topic, Popular Technical Reports.
© 2024 PatSnap. All rights reserved.Legal|Privacy policy|Modern Slavery Act Transparency Statement|Sitemap|About US| Contact US: help@patsnap.com