Axis action optimization method for six-axis robot in three-dimensional printing equipment
A six-axis robot, three-dimensional printing technology, applied in ceramic molding machines, process efficiency improvement, manufacturing tools, etc., can solve the problems of poor optimization effect, cumbersome operation, and a lot of time numerical iterative optimization, etc., to improve convenience, Improved stability, simple control method effect
- Summary
- Abstract
- Description
- Claims
- Application Information
AI Technical Summary
Problems solved by technology
Method used
Image
Examples
Embodiment 1
[0053] Specifically, such as Figure 5 ~ Figure 7 As shown, the base 0 at the root of the six-axis robot 1 is defined as the world coordinate system, and the target origin coordinate p=(x, y, z) of the target point coordinate system is determined. The X-axis direction of the target plane coordinate system is the direction of the nozzle 31 of the 3D printing head 3 . Let the Z-axis direction of the target point coordinate system be T x =(r,0,z 3 ) T , where z3 is an unknown quantity, and r is a non-zero real number, so that the Z-axis vector is parallel to the X-axis of the world coordinate system from the Top view. But not limited thereto, in other embodiments, the Z axis can also be assumed to be parallel to the Y axis of the world coordinate system or any direction. Determines the value of z3 for Tz. Since each direction axis of the target point coordinate system is vertical.
[0054] The X-axis of the target point coordinate system is perpendicular to the Z-axis of th...
PUM
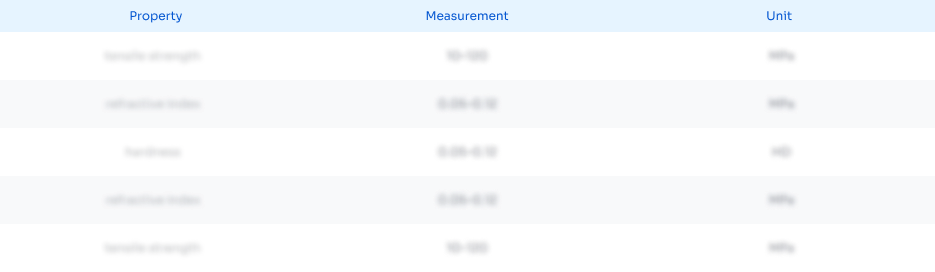
Abstract
Description
Claims
Application Information

- Generate Ideas
- Intellectual Property
- Life Sciences
- Materials
- Tech Scout
- Unparalleled Data Quality
- Higher Quality Content
- 60% Fewer Hallucinations
Browse by: Latest US Patents, China's latest patents, Technical Efficacy Thesaurus, Application Domain, Technology Topic, Popular Technical Reports.
© 2025 PatSnap. All rights reserved.Legal|Privacy policy|Modern Slavery Act Transparency Statement|Sitemap|About US| Contact US: help@patsnap.com