Moving bed reactor and use method thereof
A moving bed reactor and reactor technology, applied in chemical instruments and methods, chemical/physical processes, etc., can solve problems such as large equipment investment, low reactor space utilization, and complex operation.
- Summary
- Abstract
- Description
- Claims
- Application Information
AI Technical Summary
Problems solved by technology
Method used
Image
Examples
Embodiment 1
[0035] A moving bed reactor, with reference to figure 1 , the reactor comprises a reactor shell 13, the reactor shell 13 is provided with a catalyst loading area, the upper end of the reactor shell 13 is provided with a catalyst feed port 1, and its lower end is provided with a catalyst discharge port 9, where the catalyst feed The feed port 1 is provided with a metering buffer tank 2 and a cone valve 3 at the feed port. The catalyst discharge port 9 is provided with a discharge port cone valve 10 . The moving bed reactor is a radial reactor, and the reactor shell 13 is cylindrical.
[0036] Such as figure 2 , 3, a plurality of plate pairs and the gas-phase center tube form a structure in which the raw material flows radially, and the plate channel is the catalyst loading area and the raw material reaction area, which also has the function of heat exchange. The catalyst loading area includes a gas phase center tube 5, a plurality of plates surrounding the outside of the g...
Embodiment 2
[0038] Taking the xylene isomerization reaction as an example to further illustrate the present invention, the mixed gas of raw material liquid, high-temperature solvent and carrier gas enters the gas phase central tube 5 from the gas phase central tube inlet 4, and then distributes to each plate channel 6 to contact with the catalyst After the reaction occurs, the product enters the gas annulus 7, and then is discharged from the gas phase outlet 8 to be separated and refined downstream to obtain xylene isomerization products. If the catalyst activity cannot meet the reaction requirements, first put the regenerated or fresh catalyst into the metering buffer tank 2, open the cone valve 3 of the feed inlet and the cone valve 10 of the discharge outlet, the active life of the reaction catalyst is longer, and the intermittent Type loading and unloading, turn the gap and rotate the feeding tray 12 to the vacancy, and follow the rotation direction to the gap to rotate the discharge t...
PUM
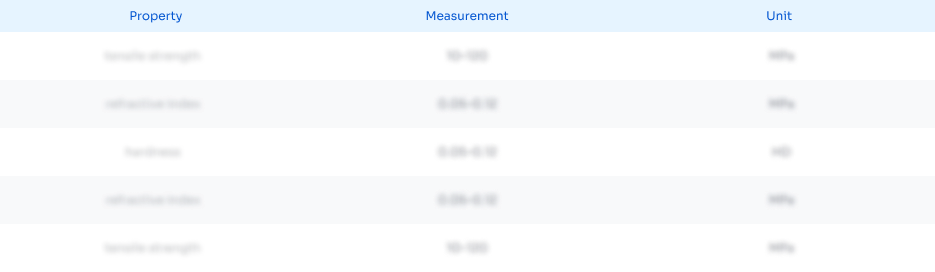
Abstract
Description
Claims
Application Information

- Generate Ideas
- Intellectual Property
- Life Sciences
- Materials
- Tech Scout
- Unparalleled Data Quality
- Higher Quality Content
- 60% Fewer Hallucinations
Browse by: Latest US Patents, China's latest patents, Technical Efficacy Thesaurus, Application Domain, Technology Topic, Popular Technical Reports.
© 2025 PatSnap. All rights reserved.Legal|Privacy policy|Modern Slavery Act Transparency Statement|Sitemap|About US| Contact US: help@patsnap.com