Phased array ultrasonic detection method for butt-weld joint of aluminum alloy sheet
A technology of ultrasonic detection and detection method, which is applied to the analysis of solids using sound waves/ultrasonic waves/infrasonic waves, material analysis using sound waves/ultrasonic waves/infrasonic waves, and measuring devices. Increased judgment, clutter, etc., to improve detection reliability, good detection effect, and avoid missed detection
- Summary
- Abstract
- Description
- Claims
- Application Information
AI Technical Summary
Problems solved by technology
Method used
Image
Examples
Embodiment 1
[0046] A phased array ultrasonic testing method for butt welds of aluminum alloy thin plates, consisting of a phased array ultrasonic instrument, a tile-shaped focused shear wave phased array probe, a phased array ultrasonic wedge, a phased array ultrasonic scanning device, and a calibration test block The main steps of the phased array ultrasonic testing system for detecting butt welds of 7mm thick aluminum alloy sheets are as follows:
[0047] S1 surface pretreatment:
[0048] Grind the scanning surface to remove foreign objects (such as welding spatter, grooves, etc.) that hinder the movement of the probe, and ensure that the surface roughness of the probe movement area is Ra≤12.5μm. The grinding range is not less than 120mm from the side edge of the weld to the outer sides. Determine the weld inspection range, and draw inspection marks and reference lines, such as figure 2 shown.
[0049] The reference line is used to guide the phased array probe to walk in the specifi...
Embodiment 2
[0072] A phased array ultrasonic testing method for butt welds of aluminum alloy thin plates, comprising a phased array ultrasonic instrument, a tile-shaped transverse wave shear wave phased array probe, a phased array ultrasonic wedge, a phased array ultrasonic scanning device, and a calibration test block Constitute a phased array ultrasonic testing system for testing 8mm-10mm thick (asymmetrical) aluminum alloy sheet butt welds, the main steps are as follows:
[0073] S1 surface pretreatment:
[0074] Grind the scanning surface to remove foreign objects (such as welding spatter, grooves, etc.) that hinder the movement of the probe, and ensure that the surface roughness of the probe movement area is Ra≤12.5μm. The grinding range extends from the side edge of the weld to the two sides of the weld for more than 6 times the thickness of the plate plus 50mm. Determine the weld inspection range, and draw inspection marks and reference lines, such as figure 2 shown.
[0075] The...
PUM
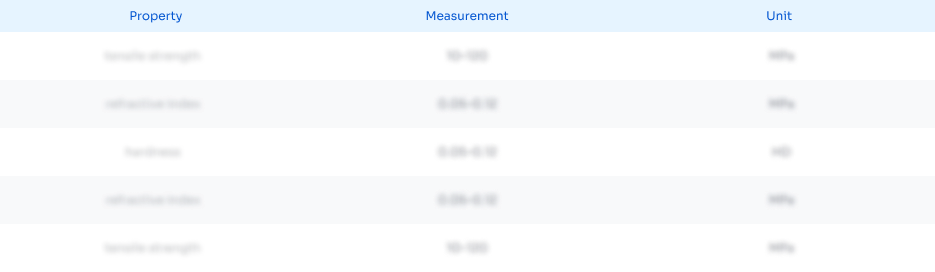
Abstract
Description
Claims
Application Information

- Generate Ideas
- Intellectual Property
- Life Sciences
- Materials
- Tech Scout
- Unparalleled Data Quality
- Higher Quality Content
- 60% Fewer Hallucinations
Browse by: Latest US Patents, China's latest patents, Technical Efficacy Thesaurus, Application Domain, Technology Topic, Popular Technical Reports.
© 2025 PatSnap. All rights reserved.Legal|Privacy policy|Modern Slavery Act Transparency Statement|Sitemap|About US| Contact US: help@patsnap.com