A bearing life cycle monitoring method based on digital twin
A full life cycle, bearing technology, applied in mechanical bearing testing, bearings, bearing assembly, etc., can solve problems such as inability to directly monitor and complex bearing damage situation, and achieve the effect of eliminating deviation, improving consistency and accurate data
- Summary
- Abstract
- Description
- Claims
- Application Information
AI Technical Summary
Problems solved by technology
Method used
Image
Examples
Embodiment Construction
[0054] The present invention is described in further detail now in conjunction with embodiment.
[0055] A method for monitoring the full life cycle of bearings based on digital twins, comprising the following steps:
[0056] Step 1: Build a bearing digital twin;
[0057] Step 2: Perform simulation correction on the established bearing digital twin in service state;
[0058] Step 3: Use the revised bearing digital twin for full life cycle monitoring and early warning.
[0059] In a specific implementation manner, Step 1 is specifically:
[0060] Step 1-1: Collect the bearing inner diameter, bearing outer diameter, bearing inner ring thickness, bearing outer ring thickness, dynamic load, static load, grease lubrication speed limit, oil lubrication speed limit, contact angle, number of rolling elements, Physical characteristics such as cage parameters and bearing assembly parameters; the bearing assembly parameters include: bearing installation position, bearing installation ac...
PUM
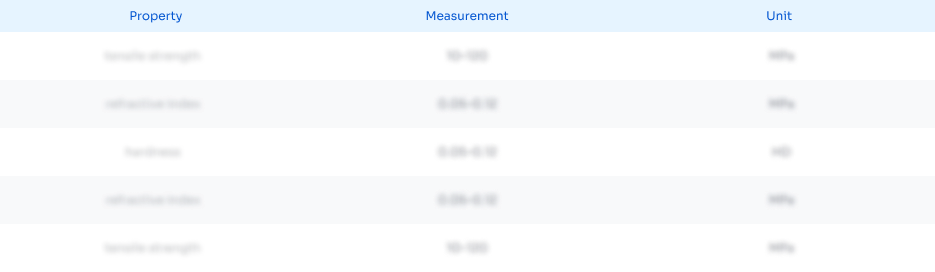
Abstract
Description
Claims
Application Information

- Generate Ideas
- Intellectual Property
- Life Sciences
- Materials
- Tech Scout
- Unparalleled Data Quality
- Higher Quality Content
- 60% Fewer Hallucinations
Browse by: Latest US Patents, China's latest patents, Technical Efficacy Thesaurus, Application Domain, Technology Topic, Popular Technical Reports.
© 2025 PatSnap. All rights reserved.Legal|Privacy policy|Modern Slavery Act Transparency Statement|Sitemap|About US| Contact US: help@patsnap.com