Organic silicon modified epoxy resin paint film and preparation method thereof
A technology of epoxy resin paint and epoxy resin, which is applied in the field of materials, can solve the problems of slow curing and molding speed, and achieve the effect of improving gloss and rapid curing and molding
- Summary
- Abstract
- Description
- Claims
- Application Information
AI Technical Summary
Problems solved by technology
Method used
Image
Examples
Embodiment 1
[0016] Organosilicon modified epoxy resin paint film comprises the following raw materials in parts by weight: 140 parts of H-type epoxy resin, 20 parts of organic silicon resin, 35 parts of polysiloxane, 25 parts of nano-calcium carbonate, 35 parts of graphene, 20 parts of ethylene glycol diglycidyl ether, 60 parts of methyl ethyl ketone.
[0017] The preparation method of silicone-modified epoxy resin paint film comprises the following steps: uniformly mix H-type epoxy resin, silicone resin and polysiloxane, heat up to 70-80°C for addition reaction for 4 hours, until the reaction is complete, Cool to room temperature; then add nano-carbonate and graphene, heat to a constant temperature of 50-60°C, drop in ethylene glycol diglycidyl ether while stirring, finish dropping within 1 hour, then add methyl ethyl ketone, and stir at room temperature for 1.2 hours, That's it.
Embodiment 2
[0019] Organosilicon modified epoxy resin paint film comprises the following raw materials in parts by weight: 130 parts of H-type epoxy resin, 10 parts of silicone resin, 30 parts of polysiloxane, 20 parts of nano iron carbonate, 30 parts of graphene, 10 parts of ethylene glycol diglycidyl ether, 40 parts of methyl ethyl ketone.
[0020] A method for preparing a silicone-modified epoxy resin paint film, comprising the following steps: uniformly mixing H-type epoxy resin, silicone resin, and polysiloxane, raising the temperature to 70-80° C. for addition reaction for 1 hour, until the reaction is complete, Cool to room temperature; then add nano-carbonate and graphene, heat to 50-60°C constant temperature, drop in ethylene glycol diglycidyl ether while stirring, finish dropping within 1h, then add methyl ethyl ketone, stir at room temperature for 1h, that is Can.
Embodiment 3
[0022] Organosilicon modified epoxy resin paint film comprises the following raw materials in parts by weight: 160 parts of H-type epoxy resin, 30 parts of organic silicon resin, 40 parts of polysiloxane, 30 parts of nano-magnesium carbonate, 40 parts of graphene, 30 parts of ethylene glycol diglycidyl ether, 80 parts of methyl ethyl ketone.
[0023] The preparation method of silicone-modified epoxy resin paint film comprises the following steps: uniformly mixing H-type epoxy resin, silicone resin and polysiloxane, raising the temperature to 70-80°C for addition reaction for 5 hours, until the reaction is complete, Cool to room temperature; then add nano-carbonate and graphene, heat to 50-60°C constant temperature, drop in ethylene glycol diglycidyl ether while stirring, finish dropping within 1 hour, then add methyl ethyl ketone, stir at room temperature for 2 hours, that is Can.
PUM
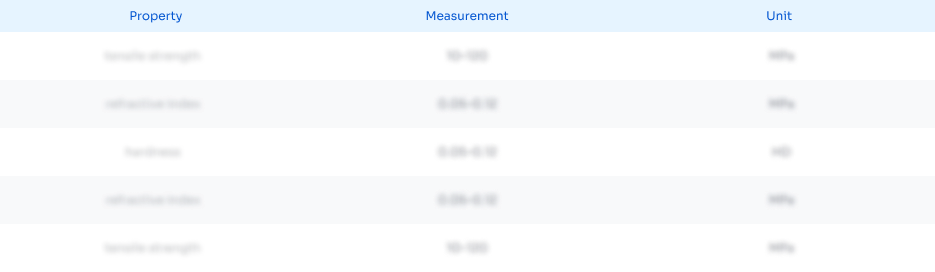
Abstract
Description
Claims
Application Information

- R&D
- Intellectual Property
- Life Sciences
- Materials
- Tech Scout
- Unparalleled Data Quality
- Higher Quality Content
- 60% Fewer Hallucinations
Browse by: Latest US Patents, China's latest patents, Technical Efficacy Thesaurus, Application Domain, Technology Topic, Popular Technical Reports.
© 2025 PatSnap. All rights reserved.Legal|Privacy policy|Modern Slavery Act Transparency Statement|Sitemap|About US| Contact US: help@patsnap.com