Double-robot collaborative curve welding planning method based on line structured light vision
A line structured light, dual-robot technology, applied in welding equipment, manipulators, program-controlled manipulators, etc., can solve the problems of low efficiency of detection methods, no planning methods constructed, and errors of theoretical models of welds.
- Summary
- Abstract
- Description
- Claims
- Application Information
AI Technical Summary
Problems solved by technology
Method used
Image
Examples
Embodiment Construction
[0051] The present invention will be further described below in conjunction with the accompanying drawings and specific preferred embodiments.
[0052] The composition of the dual-robot collaborative welding system is attached figure 2 As shown, it includes a master robot 1, a slave robot 2, a line structured light visual detection device 3, and a workpiece 4 to be welded. The end of the main robot 1 fixedly clamps the workpiece 4 to be welded, and drives the workpiece 4 to move so that the weld seam maintains a boat-shaped welding posture during welding; the welding torch 5 is installed at the end of the slave robot 2 for welding, and at the same time, the end of the robot is fixedly installed with a wire structured light The visual detection device 3, the detection device 3 includes an industrial camera 3-1 and a line structured light sensor 3-2, the line structured light emitted by the line structured light sensor 3-2 is projected onto the curved weld interface, forming a ...
PUM
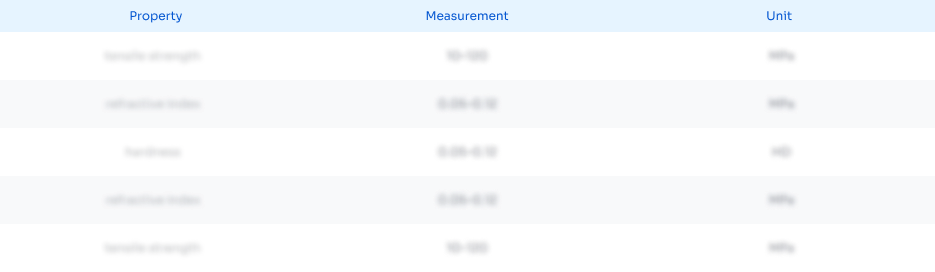
Abstract
Description
Claims
Application Information

- R&D Engineer
- R&D Manager
- IP Professional
- Industry Leading Data Capabilities
- Powerful AI technology
- Patent DNA Extraction
Browse by: Latest US Patents, China's latest patents, Technical Efficacy Thesaurus, Application Domain, Technology Topic, Popular Technical Reports.
© 2024 PatSnap. All rights reserved.Legal|Privacy policy|Modern Slavery Act Transparency Statement|Sitemap|About US| Contact US: help@patsnap.com