Composite material with polyurethane foam coated with plant fibers as well as preparation method and application thereof
A technology of polyurethane foam and plant fiber, which is applied in the field of composite materials, can solve the problems of limited use and high water absorption, and achieve the effects of avoiding painting, low hygroscopicity, and excellent corrosion resistance
- Summary
- Abstract
- Description
- Claims
- Application Information
AI Technical Summary
Problems solved by technology
Method used
Image
Examples
Embodiment 1
[0034] A kind of preparation method of the composite material of described plant fiber coating polyurethane foam, described preparation method comprises the steps:
[0035] (1) cutting the polyurethane rigid foam into a width and height size of 140mm × 40mm to obtain a polyurethane rigid foam core;
[0036] (2) The flax fibers are arranged by the rotating mandrel through the yarn arrangement system, and the plant fibers are drawn out from the outer wall of the bobbin, so that the flax fiber bundles are arranged in parallel, and the thickness of a single layer is 2 mm;
[0037] (3) Through the traction of the power system, the flax fiber and polyurethane rigid foam core material processed in step (2) are continuously fed into the starting end of the production line, and then passed through the dipping tank, guiding mold, and heating mold in turn at the end of the production line Carry out cutting, make the composite material that polyurethane rigid foam periphery coats flax fib...
Embodiment 2
[0041] A kind of preparation method of the composite material of described plant fiber coating polyurethane foam, described preparation method comprises the steps:
[0042] (1) cutting the polyurethane rigid foam into a width and height size of 140mm × 40mm to obtain a polyurethane rigid foam core;
[0043] (2) The flax fibers are arranged by the rotating mandrel through the yarn arrangement system, and the plant fibers are drawn out from the outer wall of the bobbin, so that the flax fiber bundles are arranged in parallel, and the thickness of a single layer is 2 mm;
[0044] The flax fiber has been pretreated. The pretreatment method is as follows: wash and dry the flax fiber, then alkalize it in 3% NaOH solution for 1 hour, then wash it, and then activate it in 3% cetyltrimethylammonium chloride. react in the solvent solution for 1 h.
[0045] (3) Through the traction of the power system, the flax fiber and polyurethane rigid foam core material processed in step (2) are co...
Embodiment 3
[0049] A kind of preparation method of the composite material of described plant fiber coating polyurethane foam, described preparation method comprises the steps:
[0050](1) cutting the polyurethane rigid foam into a width and height size of 140mm × 40mm to obtain a polyurethane rigid foam core;
[0051] (2) adopt rotating mandrel to carry out yarn arrangement to sisal fiber by yarn arrangement system, draw plant fiber from the yarn tube outer wall, make sisal fiber bundle arrange in parallel, single-layer thickness is 3mm;
[0052] The sisal fiber has been pretreated. The pretreatment method is as follows: the sisal fiber is washed and dried, then alkalized in 3% NaOH solution for 1h, then washed, and then chlorinated in 3% cetyl trimethyl React in ammonium active agent solution for 1h.
[0053] (3) Through the traction of the power system, the sisal fiber and polyurethane rigid foam core material processed in step (2) are continuously fed into the starting end of the prod...
PUM
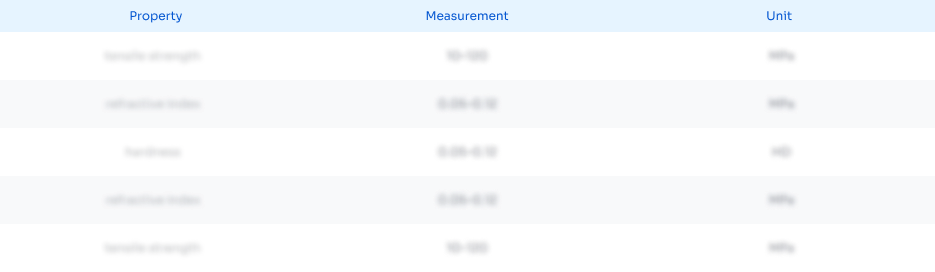
Abstract
Description
Claims
Application Information

- Generate Ideas
- Intellectual Property
- Life Sciences
- Materials
- Tech Scout
- Unparalleled Data Quality
- Higher Quality Content
- 60% Fewer Hallucinations
Browse by: Latest US Patents, China's latest patents, Technical Efficacy Thesaurus, Application Domain, Technology Topic, Popular Technical Reports.
© 2025 PatSnap. All rights reserved.Legal|Privacy policy|Modern Slavery Act Transparency Statement|Sitemap|About US| Contact US: help@patsnap.com