Carbide drill machining and manufacturing method
A cemented carbide, machining and manufacturing technology, which is applied in the field of difficult-to-machine materials in aviation and aerospace, can solve the problems of difficulty in guaranteeing aperture accuracy and surface quality, restricting the scientific research and production of difficult-to-machine materials, and poor cutting performance of materials, so as to save tool costs. and related grinding costs, improve processing efficiency and production bottlenecks, and improve the effect of drilling capacity
- Summary
- Abstract
- Description
- Claims
- Application Information
AI Technical Summary
Problems solved by technology
Method used
Image
Examples
specific Embodiment approach 1
[0037] Specific implementation mode one: combine Figure 1-Figure 2 Describe the present embodiment, the cemented carbide drill processing and manufacturing method of the present embodiment, the cemented carbide drill processing and manufacturing method, it is characterized in that:
[0038] Step 1, use a five-axis high-precision CNC tool grinder to ensure the consistency and precision of the carbide drill;
[0039] Step 2, choose the No. 46 diamond grinding wheel as the grinding tool;
[0040] In step 3, the processing parameters are selected from the cutting experiment parameters, and the optimal parameters of the experiment are: rake angle 11°, horizontal angle α of the first cutting edge, horizontal angle β of the second cutting edge, apex angle γ and lead angle 21°;
[0041] Step 4: Use small feed and multiple grinding methods to process and manufacture cemented carbide drill bits to ensure the accuracy of various angles. In the multiple grinding method, the linear speed...
PUM
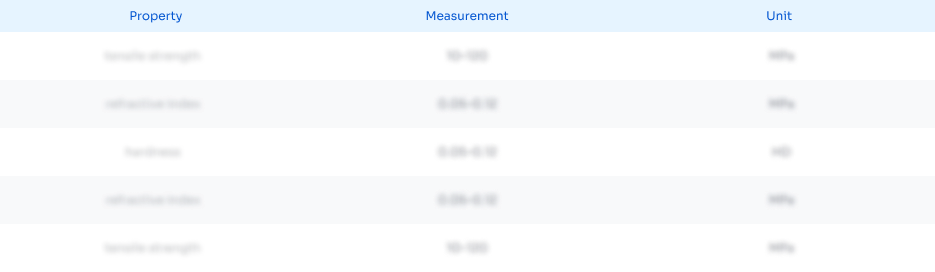
Abstract
Description
Claims
Application Information

- R&D
- Intellectual Property
- Life Sciences
- Materials
- Tech Scout
- Unparalleled Data Quality
- Higher Quality Content
- 60% Fewer Hallucinations
Browse by: Latest US Patents, China's latest patents, Technical Efficacy Thesaurus, Application Domain, Technology Topic, Popular Technical Reports.
© 2025 PatSnap. All rights reserved.Legal|Privacy policy|Modern Slavery Act Transparency Statement|Sitemap|About US| Contact US: help@patsnap.com