Novel aluminum alloy auxiliary frame
A technology of aluminum alloy and sub-frame, which is applied to vehicle parts, substructure, transportation and packaging, etc., can solve the problems of difficult quality control, many parts brackets, and many processes, saving development costs and tooling costs, guaranteeing Consistency, the effect of improving mechanical properties
- Summary
- Abstract
- Description
- Claims
- Application Information
AI Technical Summary
Problems solved by technology
Method used
Image
Examples
Embodiment 1
[0026] A new type of aluminum alloy sub-frame, including a front beam 1, a rear beam 2, a left side beam 3 and a right side beam 4, the front beam 1, rear beam 2, left side beam 3 and right side beam 4 are all made of aluminum Alloy profiles are extruded to form a hollow tubular structure;
[0027] The subframe also includes a left front mounting bracket 5, a right front mounting bracket 6, a left rear mounting bracket 7 and a right rear mounting bracket 8; the left front mounting bracket 5, the right front mounting bracket 6, the left rear mounting bracket 7 and the right rear mounting bracket The brackets 8 are all cast from aluminum alloy; the two ends of the left front mounting bracket 5, the right front mounting bracket 6, the left rear mounting bracket 7 and the right rear mounting bracket 8 are provided with assembly grooves 9;
[0028] The two ends of the front beam 1 are respectively installed in the assembly grooves 9 of the left front mounting bracket 5 and the righ...
Embodiment 2
[0030] A new type of aluminum alloy sub-frame, including a front beam 1, a rear beam 2, a left side beam 3 and a right side beam 4, the front beam 1, rear beam 2, left side beam 3 and right side beam 4 are all made of aluminum Alloy profiles are extruded to form a hollow tubular structure;
[0031] The subframe also includes a left front mounting bracket 5, a right front mounting bracket 6, a left rear mounting bracket 7 and a right rear mounting bracket 8; the left front mounting bracket 5, the right front mounting bracket 6, the left rear mounting bracket 7 and the right rear mounting bracket The brackets 8 are all cast from aluminum alloy; the two ends of the left front mounting bracket 5, the right front mounting bracket 6, the left rear mounting bracket 7 and the right rear mounting bracket 8 are provided with assembly grooves 9;
[0032] The two ends of the front beam 1 are respectively installed in the assembly grooves 9 of the left front mounting bracket 5 and the righ...
PUM
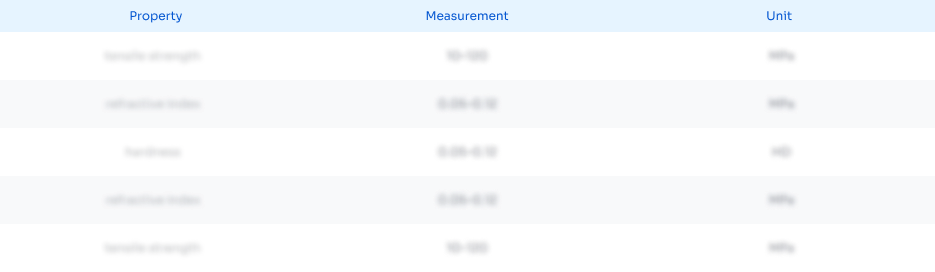
Abstract
Description
Claims
Application Information

- Generate Ideas
- Intellectual Property
- Life Sciences
- Materials
- Tech Scout
- Unparalleled Data Quality
- Higher Quality Content
- 60% Fewer Hallucinations
Browse by: Latest US Patents, China's latest patents, Technical Efficacy Thesaurus, Application Domain, Technology Topic, Popular Technical Reports.
© 2025 PatSnap. All rights reserved.Legal|Privacy policy|Modern Slavery Act Transparency Statement|Sitemap|About US| Contact US: help@patsnap.com