Steel structure profile welding method
A welding method and steel structure technology, applied in welding equipment, welding equipment, auxiliary welding equipment, etc., can solve problems that affect welding efficiency and contact end welding difficulties, so as to improve welding efficiency, facilitate turning work, and facilitate welding operations Effect
- Summary
- Abstract
- Description
- Claims
- Application Information
AI Technical Summary
Problems solved by technology
Method used
Image
Examples
Embodiment Construction
[0028] In order to make the technical means, creative features, goals and effects achieved by the present invention easy to understand, the present invention will be further described below in conjunction with specific embodiments.
[0029] see Figure 1-Figure 5 , the present invention provides a technical solution: a welding method for steel structure profiles, which uses a counter-position fixing device, which includes a first clamping mechanism 1, a second clamping mechanism 2, a first fixing plate 3, U-shaped collection box 4, U-shaped fixed frame 5, first lifting cylinder 6, push rod 7 and second fixed plate 8, two second fixed plates 8 arranged horizontally and transversely are symmetrically installed on the upper right side of U-shaped collection box 4, and pass The U-shaped collection box 4 provides an installation carrier for the first lifting cylinder 6, and also effectively collects the welding slag generated by welding. The two second fixing plates 8 are equidista...
PUM
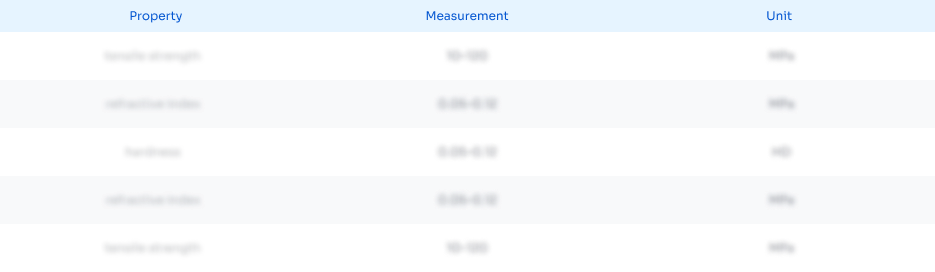
Abstract
Description
Claims
Application Information

- Generate Ideas
- Intellectual Property
- Life Sciences
- Materials
- Tech Scout
- Unparalleled Data Quality
- Higher Quality Content
- 60% Fewer Hallucinations
Browse by: Latest US Patents, China's latest patents, Technical Efficacy Thesaurus, Application Domain, Technology Topic, Popular Technical Reports.
© 2025 PatSnap. All rights reserved.Legal|Privacy policy|Modern Slavery Act Transparency Statement|Sitemap|About US| Contact US: help@patsnap.com