Nickel smelting device and nickel smelting method
A technology of nickel matte and smelting zone, which is applied in the field of nickel smelting equipment, can solve the problems of adding large vulcanizing agent, poor dilution effect, complicated process, etc., and achieves the effects of good environmental protection conditions, stable production, and simple operation
- Summary
- Abstract
- Description
- Claims
- Application Information
AI Technical Summary
Problems solved by technology
Method used
Image
Examples
Embodiment 1
[0063] use figure 1 The shown nickel smelting device processes nickel concentrate, and the structural parameters are as follows: Among them, L’ / L is 0.12; L 1 : L 2 :L 3 It is 18: 6: 9 (the definitions of each letter are the same as above). The nickel smelting steps are as follows:
[0064] S1, dry and finely grind nickel concentrate (containing Ni8.91%, containing Cu 5.35%, containing 0.35% Co, containing Fe35.77%, containing MgO7.89%), quartz sand flux, soot and launder shell After being mixed, it is used as nickel-smelting raw material, sprayed into the furnace through the concentrate nozzle, the particle size of the raw material is ≤1mm, and the ratio is concentrate: flux: return material = 100: 26: 7.6.
[0065] S2, nickel smelting raw materials enter the flash smelting reaction tower, and undergo flash smelting reaction in the presence of the first oxygen-enriched air (oxygen volume content is 80%) to generate smelting products and smelting flue gas, flash smelting r...
Embodiment 2
[0072] use figure 1 The shown nickel smelting device processes nickel concentrate, and the structural parameters are as follows: Among them, L’ / L is 0.14; L 1 : L 2 :L 3 It is 18: 8: 9 (the definitions of each letter are the same as above). The nickel smelting steps are as follows:
[0073] S1, dry and finely grind nickel concentrate (containing 13% Ni, 1.35% Cu, 0.4% Co, 37% Fe, 1.3% MgO), quartz sand flux, and system return materials to be used as nickel smelting The raw material is sprayed into the furnace through the concentrate nozzle, the particle size of the raw material is ≤1mm, and the ratio is concentrate: flux: return material = 100: 28: 7.5.
[0074] S2, nickel smelting raw materials enter the flash smelting reaction tower, and undergo flash smelting reaction in the presence of the first oxygen-enriched air (oxygen volume content is 80%) to generate smelting products and smelting flue gas, flash smelting reaction tower The temperature of the inner cavity is 14...
Embodiment 3
[0081] use figure 1 The shown nickel smelting device processes nickel concentrate, and the structural parameters are as follows: Among them, the sedimentation tank does not have a spray gun, and L1:L2:L3 is 18:6:9 (the definitions of each letter are the same as above). The nickel smelting steps are as follows:
[0082] S1, dry and finely grind nickel concentrate (containing 5.25% Ni, 4.6% Cu, 0.34% Co, 41% Fe, 7.85% MgO), quartz sand flux, and system return material to be used as nickel refining The raw material is sprayed into the furnace through the concentrate nozzle, the particle size of the raw material is ≤1mm, and the ratio is concentrate: flux: return material = 100: 33: 7.5.
[0083] S2, nickel smelting raw materials enter the flash smelting reaction tower, and undergo flash smelting reaction in the presence of the first oxygen-enriched air (oxygen volume content is 80%) to generate smelting products and smelting flue gas, flash smelting reaction tower The temperatu...
PUM
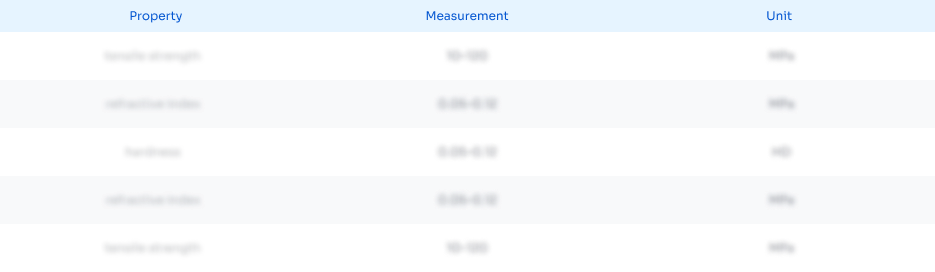
Abstract
Description
Claims
Application Information

- R&D Engineer
- R&D Manager
- IP Professional
- Industry Leading Data Capabilities
- Powerful AI technology
- Patent DNA Extraction
Browse by: Latest US Patents, China's latest patents, Technical Efficacy Thesaurus, Application Domain, Technology Topic, Popular Technical Reports.
© 2024 PatSnap. All rights reserved.Legal|Privacy policy|Modern Slavery Act Transparency Statement|Sitemap|About US| Contact US: help@patsnap.com