Preparation method of star-shaped bismuth vanadate/boron alkene composite material
A star-shaped bismuth vanadate and composite material technology is applied in chemical instruments and methods, chemical/physical processes, physical/chemical process catalysts, etc., to achieve the effects of simple and easy preparation methods, uniform morphology, and improved photocatalytic performance.
- Summary
- Abstract
- Description
- Claims
- Application Information
AI Technical Summary
Problems solved by technology
Method used
Image
Examples
Embodiment 1
[0032] A method of preparing a star-shaped vanadate / bohane composite material comprising the steps of:
[0033] Step 1, 80mg of BI (NO 3 ) 3 · 5h 2 O Add to 40 ml of deionized water, then dissolve, then add 120 mg of NA 3 VO 4 12h 2 O-above solutions, after ultrasonic dissolution, transferred in a hydrothermal reaction kettle, 150 ° C for 8 hours, cooled to room temperature, and then cleaned with ethanol, 60 ° C, to obtain bismuth-shaped vanadate;
[0034] Step 2, the star-shaped vanadate obtained by step 1 is added 60 mg to 100 mL of aqueous wetting dispersant AQ-32 (Disburron), ultrasonic dispersion, and obtain dispersion;
[0035] Step 3, 10 mg of bohane is added to the dispersion obtained in step 2, and the ultrasonic dispersion is transferred to the hydrothermal reaction kettle, 120 ° C for 12 hours, cooled to room temperature, washed with deionized water and ethanol, dried 100 ° C To obtain a bismuth / bohane composite mixture of a star-shaped vanadate;
[0036] Step 4, a ...
Embodiment 2
[0038] A method of preparing a star-shaped vanadate / bohane composite material comprising the steps of:
[0039] Step 1, 60mg of BI (NO 3 ) 3 · 5h 2 O Add to 40 ml of deionized water, then dissolve, then add 100 mg of NA 3 VO 4 12h 2 O to the above solution, after the ultrasonic dissolution, transferred to the hydrothermal reaction kettle, 160 ° C for 8 hours, cooled to room temperature, and then washed by deionized water, dried at 80 ° C to obtain bismuth-shaped vanadate;
[0040] Step 2, the star-shaped vanadate obtained by step 1 was 40 mg of 40 mg of 40 mL aqueous wetting dispersant DISPERBYK-190, and the ultrasonic dispersion was obtained.
[0041] Step 3, 1 mg of bohane is added to the dispersion obtained in step 2, and the ultrasonic dispersion is transferred to the hydrothermal reaction kettle, 10 hours at 130 ° C, cooled to room temperature, washed with deionized water and ethanol, 80 ° C drying To obtain a bismuth / bohane composite mixture of a star-shaped vanadate;
...
Embodiment 3
[0044] A method of preparing a star-shaped vanadate / bohane composite material comprising the steps of:
[0045] Step 1, 80mg of BI (NO 3 ) 3 · 5h 2 O Add to 40 ml of deionized water, then dissolve, then add 120 mg of NA 3 VO 4 12h 2 O-above solutions, after ultrasonic dissolution, transferred in a hydrothermal reaction kettle, 150 ° C for 8 hours, cooled to room temperature, and then cleaned with ethanol, 60 ° C, to obtain bismuth-shaped vanadate;
[0046] Step 2, the star-shaped vanadate obtained by step 1 is added 60 mg to 100 mL of aqueous wetting dispersant AQ-32 (Disburron), ultrasonic dispersion, and obtain dispersion;
[0047] Step 3, 10 mg of bohane is added to the dispersion obtained in step 2, and the ultrasonic dispersion is transferred to the hydrothermal reaction kettle, 120 ° C for 12 hours, cooled to room temperature, washed with deionized water and ethanol, dried 100 ° C To obtain a bismuth / bohane composite mixture of a star-shaped vanadate;
[0048] Step 4, a ...
PUM
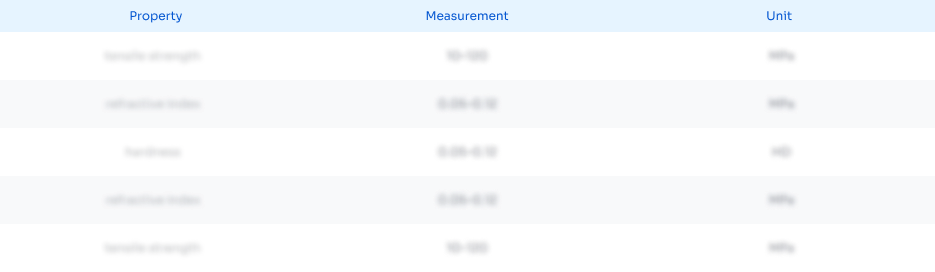
Abstract
Description
Claims
Application Information

- R&D
- Intellectual Property
- Life Sciences
- Materials
- Tech Scout
- Unparalleled Data Quality
- Higher Quality Content
- 60% Fewer Hallucinations
Browse by: Latest US Patents, China's latest patents, Technical Efficacy Thesaurus, Application Domain, Technology Topic, Popular Technical Reports.
© 2025 PatSnap. All rights reserved.Legal|Privacy policy|Modern Slavery Act Transparency Statement|Sitemap|About US| Contact US: help@patsnap.com