Online denitration process for sintering flue gas
A technology for sintering flue gas and denitrification, applied in the field of industrial flue gas purification process and sintering flue gas online denitrification process, can solve the problems of difficult disposal of waste catalyst, high operating cost, large denitration investment, etc. The effect of large diameter and low gas resistance
- Summary
- Abstract
- Description
- Claims
- Application Information
AI Technical Summary
Problems solved by technology
Method used
Image
Examples
Embodiment 1
[0086] see figure 1 , taking a steel factory 450m 2 Take the sintering machine as an example, the sintering machine has 24 groups (48 pieces) of bellows 12 in total. Including the sintering air flow passing through the sintering material under the suction action of the fan (including the external exhaust gas fan 21-1, the high NOx flue gas fan 21-2, the desulfurization flue gas fan 21-3, and the low temperature flue gas fan 21-4) Layer 2, bottoming material 2.1, sintering machine 1 trolley 1.1 grate, bellows 12 below trolley 1.1 enter the main flue (including high temperature flue gas main flue 16-1, high NOx flue gas main flue 16-2, low temperature flue gas Gas main flue 16-3); along the traveling direction of 1 trolley 1.1 of the sintering machine, the sintering machine is divided into five areas: ignition area, low-temperature flue gas area, rapid flue gas heating area, NOx concentration rapid reduction area and high-temperature flue gas area area. The sintering mixture ...
Embodiment 2
[0094] see figure 2 , taking a steel factory 450m 2 Take the belt-type sintering machine as an example, the sintering machine has 24 groups (48 pieces) of bellows 12 in total. Adjust the operating process parameters of the sintering machine 1, reduce the thickness of the sintering material layer 2 by 10%, from the original 800mm to 720mm, or reduce the travel speed of the sintering machine trolley 1.1 by 10%, and correspondingly reduce the number of fans (including the exhaust gas fan) 21-1, high NOx flue gas blower 21-2, desulfurization flue gas blower 21-3, low temperature flue gas blower 21-4) extraction volume. By adjusting and changing the relative lengths of the ignition area, low temperature flue gas area, flue gas rapid temperature rise area, NOx concentration rapid reduction area and high temperature flue gas area of the original sintering machine, the length of the adjusted high temperature flue gas area is increased to the sintering machine 1 is 40-45% of the t...
PUM
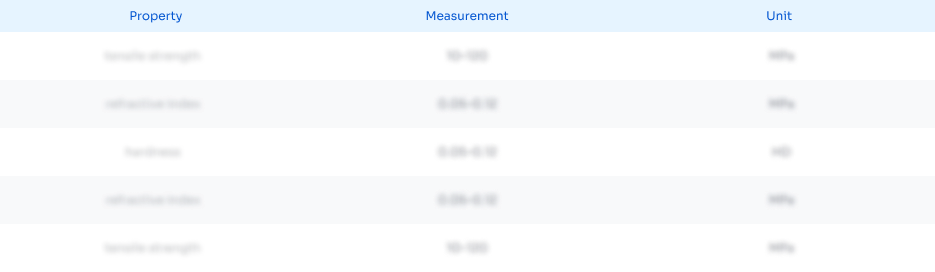
Abstract
Description
Claims
Application Information

- Generate Ideas
- Intellectual Property
- Life Sciences
- Materials
- Tech Scout
- Unparalleled Data Quality
- Higher Quality Content
- 60% Fewer Hallucinations
Browse by: Latest US Patents, China's latest patents, Technical Efficacy Thesaurus, Application Domain, Technology Topic, Popular Technical Reports.
© 2025 PatSnap. All rights reserved.Legal|Privacy policy|Modern Slavery Act Transparency Statement|Sitemap|About US| Contact US: help@patsnap.com