Variable-rigidity sandwich composite material structure based on 3D printing and forming method thereof
A 3D printing and composite material technology, which is applied in the field of variable stiffness sandwich composite material structure and its forming, can solve the problems of inability to achieve variable stiffness, differences in the shape and size of parts, and difficulty in accurately controlling the shape of the sandwich structure.
- Summary
- Abstract
- Description
- Claims
- Application Information
AI Technical Summary
Problems solved by technology
Method used
Image
Examples
Embodiment 1
[0043] see Figure 5 , a 3D printing-based variable stiffness sandwich composite structure forming method, mainly includes the following steps:
[0044] 1) Use the 3D modeling software Solidworks to establish a 3D model of the "L" sandwich structure, import the model into ANSYS finite element software for analysis, and load the boundary load force F, it can be concluded that there is a stress concentration at the right angle part, and the most Start destroying first. Therefore, in order to improve the structural strength, the core material (4) at the right angle part is densely designed, so that it forms a gradient distribution from dense to sparse with the core material (3) at the planar part.
[0045] 2) Select the multi-tow automatic placement equipment to prepare the lower panel (1) and upper panel (2) of the sandwich structure, and generate the processing track; select the continuous fiber additive manufacturing equipment with a printing diameter of 1 mm to prepare the c...
PUM
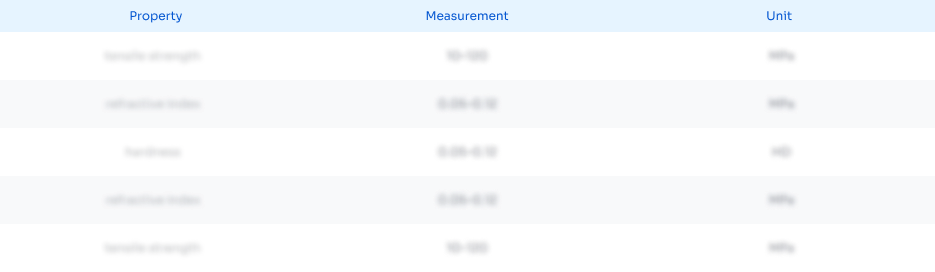
Abstract
Description
Claims
Application Information

- R&D
- Intellectual Property
- Life Sciences
- Materials
- Tech Scout
- Unparalleled Data Quality
- Higher Quality Content
- 60% Fewer Hallucinations
Browse by: Latest US Patents, China's latest patents, Technical Efficacy Thesaurus, Application Domain, Technology Topic, Popular Technical Reports.
© 2025 PatSnap. All rights reserved.Legal|Privacy policy|Modern Slavery Act Transparency Statement|Sitemap|About US| Contact US: help@patsnap.com