Liquid crystal backlight light guide plate self-adhesive protective film and production method thereof
A technology of self-adhesive protective film and production method, applied in the direction of adhesives, adhesive types, other rubber adhesives, etc., can solve the problems of affecting the light-emitting effect of the light guide plate, the light guide plate cannot be used, and the residual glue of the light guide plate, etc., to achieve Good anti-sticking effect, easy processing, and the effect of reducing production costs
- Summary
- Abstract
- Description
- Claims
- Application Information
AI Technical Summary
Problems solved by technology
Method used
Image
Examples
Embodiment 1
[0034] S1. Weigh the self-adhesive layer 1 including 75 parts by mass of polyethylene and 25 parts by mass of soft rubber resin, the middle layer 2 includes 50 parts by mass of low-density polypropylene and 50 parts by mass of high-density polyethylene, and the unwinding layer 3 includes 50 parts by mass of Part block copolymer polypropylene, 50 parts by mass of low density polyethylene and 2 parts by mass of opening agent, and then the materials contained in self-adhesive layer 1, middle layer 2 and unwinding layer 3 are respectively put into multi-layer co-extrusion casting In the suction barrel corresponding to the casting machine, the vacuum negative pressure of the casting machine is transported to the extruder hopper of the casting machine to be plasticized into a melt;
[0035] S2, the melt in step S1 is extruded through the screw rod of the extruder, then filtered by a filter, distributed to the die head through a distributor, and cooled by a casting roll and a cooling ...
Embodiment 2
[0038]S1. Weigh the self-adhesive layer 1 including 70 parts by mass of polyethylene and 30 parts by mass of soft rubber resin, the middle layer 2 includes 45 parts by mass of low-density polypropylene and 55 parts by mass of high-density polyethylene, and the unwinding layer 3 includes 49 parts by mass Part block copolymerized polypropylene, 48 parts by mass of low density polyethylene and 3 parts by mass of opening agent, and then the materials contained in self-adhesive layer 1, middle layer 2 and unwinding layer 3 are respectively put into multi-layer co-extrusion casting In the suction barrel corresponding to the casting machine, the vacuum negative pressure of the casting machine is transported to the extruder hopper of the casting machine to be plasticized into a melt;
[0039] S2, the melt in step S1 is extruded through the screw rod of the extruder, then filtered by a filter, distributed to the die head through a distributor, and cooled by a casting roll and a cooling ...
Embodiment 3
[0042] S1. Weigh the self-adhesive layer 1 including 80 parts by mass of polyethylene and 20 parts by mass of soft rubber resin, the middle layer 2 includes 55 parts by mass of low-density polypropylene and 45 parts by mass of high-density polyethylene, and the unwinding layer 3 includes 50 parts by mass of Part block copolymer polypropylene, 50 parts by mass of low density polyethylene and 3 parts by mass of opening agent, and then the materials contained in the self-adhesive layer 1, the middle layer 2 and the unwinding layer 3 are respectively put into the multi-layer co-extrusion cast In the suction barrel corresponding to the casting machine, the vacuum negative pressure of the casting machine is transported to the extruder hopper of the casting machine to be plasticized into a melt;
[0043] S2, the melt in step S1 is extruded through the screw rod of the extruder, then filtered by a filter, distributed to the die head through a distributor, and cooled by a casting roll a...
PUM
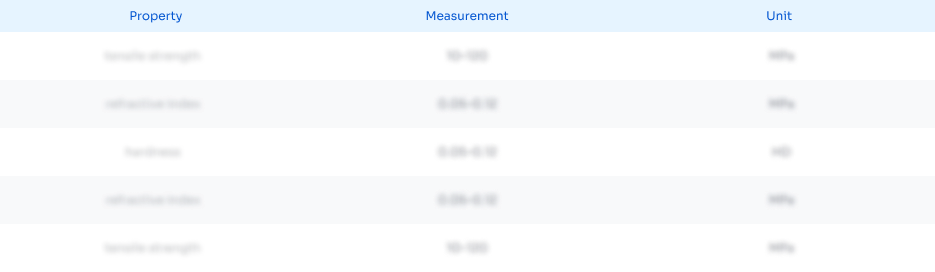
Abstract
Description
Claims
Application Information

- R&D
- Intellectual Property
- Life Sciences
- Materials
- Tech Scout
- Unparalleled Data Quality
- Higher Quality Content
- 60% Fewer Hallucinations
Browse by: Latest US Patents, China's latest patents, Technical Efficacy Thesaurus, Application Domain, Technology Topic, Popular Technical Reports.
© 2025 PatSnap. All rights reserved.Legal|Privacy policy|Modern Slavery Act Transparency Statement|Sitemap|About US| Contact US: help@patsnap.com