Electric arc additive manufacturing method based on reverse compensation
A technology of additive manufacturing and reverse compensation, applied in additive manufacturing, additive processing, etc., can solve the problems of the size and structural accuracy of formed parts, etc., and achieve strong structural designability, active control, and reduction of welding. deformation effect
- Summary
- Abstract
- Description
- Claims
- Application Information
AI Technical Summary
Problems solved by technology
Method used
Image
Examples
Embodiment 1
[0036] Such as Figure 1-7 As shown, a reverse compensation-based arc additive manufacturing method specifically includes the following steps:
[0037] Step 1: Establish a 3D model of the additive part, pre-process the 3D model, and then import it into the finite element analysis software for thermal coupling analysis; according to the actual process flow of the arc additive manufacturing, establish a digital model of the additive part in the 3D software The 3D model is imported into the finite element analysis software, the model is preprocessed by the finite element analysis software, the heat source subroutine is written, and the thermal-mechanical coupling analysis is performed on the 3D model to obtain the stress field, temperature field and shape after the initial additive manufacturing. variable.
[0038] Step 2: Pre-process the model and simulate it to extract the thermal stress and deformation of the substrate deposited by the interpass material;
[0039] Step 3: Im...
PUM
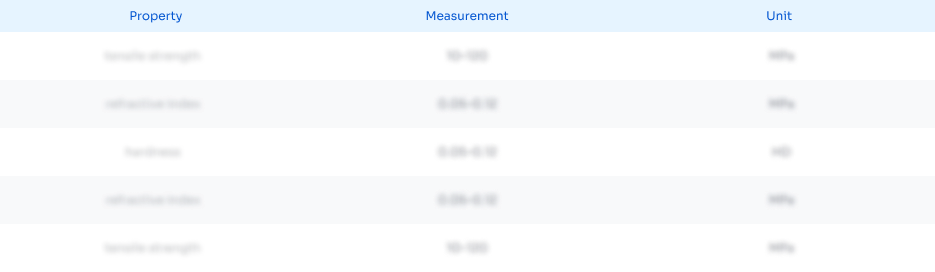
Abstract
Description
Claims
Application Information

- R&D Engineer
- R&D Manager
- IP Professional
- Industry Leading Data Capabilities
- Powerful AI technology
- Patent DNA Extraction
Browse by: Latest US Patents, China's latest patents, Technical Efficacy Thesaurus, Application Domain, Technology Topic, Popular Technical Reports.
© 2024 PatSnap. All rights reserved.Legal|Privacy policy|Modern Slavery Act Transparency Statement|Sitemap|About US| Contact US: help@patsnap.com