Heat treatment process for steel structure machining
A machining and steel structure technology, applied in the field of heat treatment, can solve the problem of high energy consumption, achieve the effect of avoiding excessive energy consumption and improving heat utilization
- Summary
- Abstract
- Description
- Claims
- Application Information
AI Technical Summary
Problems solved by technology
Method used
Examples
Embodiment Construction
[0010] According to the above-mentioned characteristics of the application, the implementation mode of the application is further described:
[0011] This embodiment provides a heat treatment process for steel structure machining, which includes the following steps: S1 heat-treat the workpiece in a salt bath furnace at 150-450°C for the first stage; Cool to room temperature; S3 heat the workpiece in a salt bath furnace at 550-800°C for the second stage;
[0012] S4 heat preservation time is 48 hours, and then oil-cooled to room temperature in the air; S5 conducts the first-stage cold treatment of the workpiece in liquid nitrogen; S6 conducts the third-stage heat treatment of the workpiece in a salt bath furnace at 550-800 °C; S7 heat preservation The time is 48 hours, and then oil-cooled to room temperature in the air; S8, the workpiece is heated in the fourth stage in a salt bath furnace at 150-450 °C; S9, the holding time is 48 hours, and then oil-cooled to room temperature ...
PUM
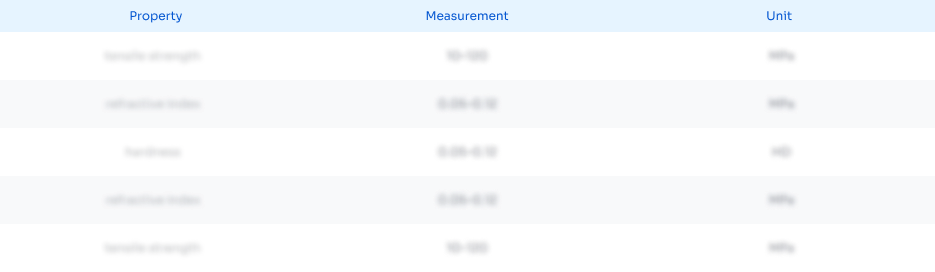
Abstract
Description
Claims
Application Information

- R&D
- Intellectual Property
- Life Sciences
- Materials
- Tech Scout
- Unparalleled Data Quality
- Higher Quality Content
- 60% Fewer Hallucinations
Browse by: Latest US Patents, China's latest patents, Technical Efficacy Thesaurus, Application Domain, Technology Topic, Popular Technical Reports.
© 2025 PatSnap. All rights reserved.Legal|Privacy policy|Modern Slavery Act Transparency Statement|Sitemap|About US| Contact US: help@patsnap.com