Intelligent elastic bearing and control method
An intelligent elastic and bearing technology, which is applied to bearings, bearing components, shafts and bearings, etc., can solve problems such as not being able to actively adapt to changes in load
- Summary
- Abstract
- Description
- Claims
- Application Information
AI Technical Summary
Problems solved by technology
Method used
Image
Examples
Embodiment 1
[0025] Example 1: Combining figure 1 This embodiment will be described. This embodiment is a spherical tapered intelligent elastic bearing, which specifically includes: a first joint 1, a second joint 2, and a transition layer; the transition layer includes several piezoelectric polymer material layers 3 and several metal layers 4, and the compression The electropolymer material layers 3 and the metal layers 4 are alternately stacked. The first joint 1, the second joint 2, and the transition layer are bonded together by gluing, vulcanization and other technologies. Wherein the piezoelectric polymer material layer 3 and the metal layer 4 are stacked alternately, and keep concentricity and the thickness of each part of the same layer is uniform.
[0026] In the embodiment, the transition layer is a spherical cone, the first joint 1 and the second joint 2 are both circular flanges, and the diameter of the first joint 1 is smaller than the diameter 2 of the second joint; piezoel...
Embodiment 2
[0028] Embodiment 2: This embodiment is a spherical tapered intelligent elastic bearing, which adopts magnetorheological elastomer material and overlaps the metal layer, and other components and connection methods are the same as those in Embodiment 1. When the intelligent elastic bearing works, a magnetic field is applied to the magnetorheological elastomer material layer. When the external load changes, the intelligent elastic bearing controls the change of the external magnetic field, so that the magnetorheological elastomer material layer generates active force under the drive of the magnetic field to resist the external load and realize the active vibration reduction of the helicopter rotor system.
Embodiment 3
[0029] Embodiment 3: This embodiment is a spherical tapered intelligent elastic bearing, which uses a shape memory polymer material to overlap with a metal layer, and other components and connection methods are the same as in Embodiment 1. When the smart elastic bearing works, a temperature field is applied to the shape memory polymer material layer. When the external load changes, the intelligent elastic bearing controls the change of the external temperature, so that the shape memory polymer material layer generates active force under the drive of the temperature field to resist the external load and realize the active vibration reduction of the helicopter rotor system.
PUM
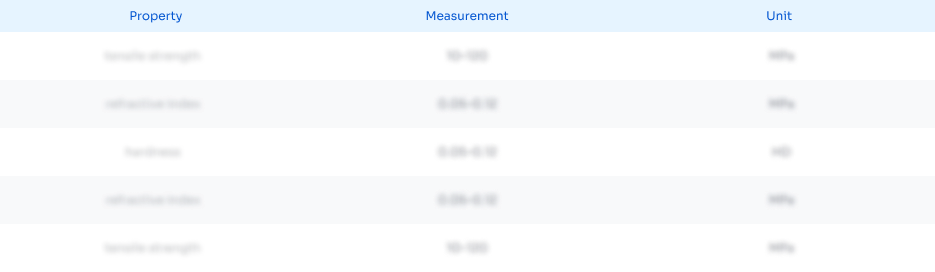
Abstract
Description
Claims
Application Information

- R&D
- Intellectual Property
- Life Sciences
- Materials
- Tech Scout
- Unparalleled Data Quality
- Higher Quality Content
- 60% Fewer Hallucinations
Browse by: Latest US Patents, China's latest patents, Technical Efficacy Thesaurus, Application Domain, Technology Topic, Popular Technical Reports.
© 2025 PatSnap. All rights reserved.Legal|Privacy policy|Modern Slavery Act Transparency Statement|Sitemap|About US| Contact US: help@patsnap.com