Novel flange production process
A production process and flange technology, applied in flange connection, pipe/pipe joint/pipe fitting, through components, etc., can solve the problems of high labor cost, long milling time, material loss, etc., to improve the overall accuracy and use range. The effect of wide and yield improvement
- Summary
- Abstract
- Description
- Claims
- Application Information
AI Technical Summary
Problems solved by technology
Method used
Examples
Embodiment 1
[0019] A kind of novel flange production technique described in the present invention described in the present invention, it comprises the following steps,
[0020] (1) Send the raw materials into the primary smelting furnace for primary smelting. The initial smelting temperature is 1110°C, and the initial smelting is 60 minutes. When it reaches 23kPa, carry out oxygen blowing decarburization, adjust the vacuum degree to 140Pa, add a deoxidizer to the VOD ladle under vacuum conditions for deoxidation, and finally hang out the VOD ladle for pouring. The pouring temperature is 1300°C and the pouring speed is 29kg / s , the pouring time is 20s, and the billet is obtained;
[0021] (2) Forging the billet, the initial forging temperature is controlled at 1130°C, and the final forging temperature is controlled at 780°C. After forging, the billet is air-cooled to 570°C, then placed in a heating furnace and heated to 915°C, and then air-cooled to 450°C. Finally adopt water to cool to r...
Embodiment 2
[0032] A kind of novel flange production technique described in the present invention described in the present invention, it comprises the following steps,
[0033] (1) Send the raw materials into the primary smelting furnace for primary smelting. The initial smelting temperature is 1050°C, and the initial smelting is 60 minutes. When it reaches 22kPa, carry out oxygen blowing decarburization, adjust the vacuum degree to 130Pa, add a deoxidizer to the VOD ladle under vacuum conditions for deoxidation, and finally hang out the VOD ladle for pouring. The pouring temperature is 1250°C and the pouring speed is 24kg / s , the pouring time is 20s, and the billet is obtained;
[0034] (2) Forging the billet, the initial forging temperature is controlled at 1110°C, and the final forging temperature is controlled at 760°C. After forging, the billet is air-cooled to 540°C, then placed in a heating furnace and heated to 905°C, and then air-cooled to 440°C. Finally adopt water to cool to r...
PUM
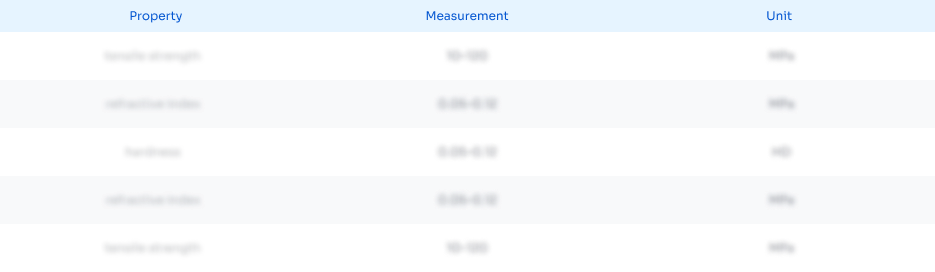
Abstract
Description
Claims
Application Information

- R&D Engineer
- R&D Manager
- IP Professional
- Industry Leading Data Capabilities
- Powerful AI technology
- Patent DNA Extraction
Browse by: Latest US Patents, China's latest patents, Technical Efficacy Thesaurus, Application Domain, Technology Topic, Popular Technical Reports.
© 2024 PatSnap. All rights reserved.Legal|Privacy policy|Modern Slavery Act Transparency Statement|Sitemap|About US| Contact US: help@patsnap.com