Production process of curing agent for yarn impregnation
A production process and curing agent technology, applied in antimonate/antimonite and other directions, can solve the problems of complex impurity removal process, high raw material cost, low product purity, etc., and achieve simple raw materials, low equipment requirements, and product purity. high effect
- Summary
- Abstract
- Description
- Claims
- Application Information
AI Technical Summary
Problems solved by technology
Method used
Image
Examples
Embodiment 1
[0025] Such as figure 1 Shown a kind of production process of curing agent for yarn dipping, the specific production process is as follows:
[0026] S1: Preparation of sodium pyroantimonate: Add sodium hydroxide and water to the reaction kettle, then add antimony trioxide, and react at a constant temperature of 80-120°C for 2 hours; cool down to 30-50°C, and inject ozone while stirring to carry out Oxidation reaction for 5 hours; then heat up to 100°C, stand for crystallization, centrifuge, and dry to obtain sodium pyroantimonate;
[0027] S2: Preparation of hexafluoroantimonic acid: at 60-120°C, mix antimony trioxide with acetic acid solution containing hydrogen fluoride, then add hydrogen peroxide dropwise at a rate of 5mL / min while stirring, and obtain hexafluoroantimony after the reaction is complete acid solution;
[0028] S3: Preparation of silver hexafluoroantimonate mother liquor: under the condition of 60-120°C, equimolar amounts of sodium pyroantimonate solid and s...
Embodiment 2
[0035] Such as figure 1 Shown a kind of production process of curing agent for yarn dipping, the specific production process is as follows:
[0036] S1: Preparation of sodium pyroantimonate: Add sodium hydroxide and water to the reaction kettle, then add antimony trioxide, and react at a constant temperature of 80-120°C for 3 hours; cool down to 50°C, and introduce ozone while stirring to carry out oxidation reaction 6 hours; then heat up to 100°C, stand for crystallization, centrifuge, and dry to obtain sodium pyroantimonate;
[0037] S2: Preparation of hexafluoroantimonic acid: at 60-120°C, mix antimony trioxide with acetic acid solution containing hydrogen fluoride, then add hydrogen peroxide dropwise at a rate of 15mL / min while stirring, and obtain hexafluoroantimony after the reaction is complete acid solution;
[0038] S3: Preparation of silver hexafluoroantimonate mother liquor: under the condition of 60-120°C, equimolar amounts of sodium pyroantimonate solid and silv...
PUM
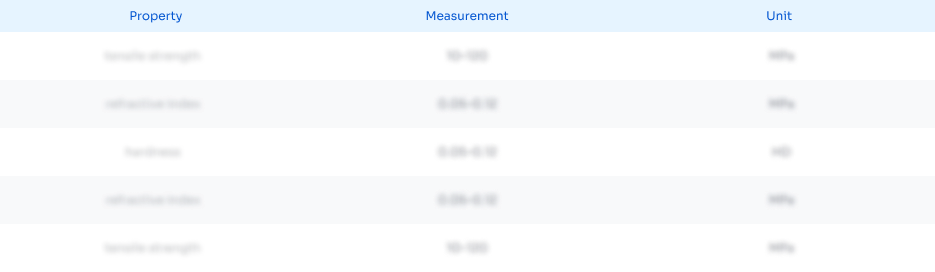
Abstract
Description
Claims
Application Information

- R&D Engineer
- R&D Manager
- IP Professional
- Industry Leading Data Capabilities
- Powerful AI technology
- Patent DNA Extraction
Browse by: Latest US Patents, China's latest patents, Technical Efficacy Thesaurus, Application Domain, Technology Topic, Popular Technical Reports.
© 2024 PatSnap. All rights reserved.Legal|Privacy policy|Modern Slavery Act Transparency Statement|Sitemap|About US| Contact US: help@patsnap.com