Mask plate cleaning method and device
A mask plate and cleaning agent technology, applied in the field of mask plate cleaning methods and devices, can solve the problems of poor elution effect of a single organic solvent, inability to recycle the medicinal solution, and easily confused classification, and reduce solvent consumption. amount, eliminate superficial effects, reduce the effect of variety and quantity
- Summary
- Abstract
- Description
- Claims
- Application Information
AI Technical Summary
Problems solved by technology
Method used
Image
Examples
Embodiment 1
[0056] A method for cleaning a mask plate, the mask plate being a metal mask plate, the cleaning method comprising the following steps:
[0057] S110, putting the mask plate to be cleaned into an organic cleaning agent for ultrasonic immersion cleaning.
[0058] Specifically, the mask plate to be cleaned is sequentially put into the first ultrasonic soaking tank 110, the second ultrasonic soaking tank 120 and the third ultrasonic soaking tank 130 all filled with the organic cleaning agent, and ultrasonic soaking is carried out. cleaning. The ultrasonic soaking and cleaning conditions of the first ultrasonic soaking tank 110 , the second ultrasonic soaking tank 120 and the third ultrasonic soaking tank 130 are: power 3kw, time 8min, frequency 80kHz.
[0059] S120 , cleaning the soaked and cleaned mask with ultrasonic vibration using the organic cleaning agent.
[0060] Specifically, the soaked and cleaned mask plates are sequentially put into the first ultrasonic shaking clea...
Embodiment 2
[0067] A method for cleaning a mask plate, the mask plate is an In (indium) mask plate, and the cleaning method comprises the following steps:
[0068] S210, putting the mask plate to be cleaned into an organic cleaning agent for ultrasonic immersion cleaning.
[0069] Specifically, the mask plate to be cleaned is sequentially put into the first ultrasonic soaking tank 110, the second ultrasonic soaking tank 120 and the third ultrasonic soaking tank 130 all filled with the organic cleaning agent, and ultrasonic soaking is carried out. cleaning. The ultrasonic soaking and cleaning conditions of the first ultrasonic soaking tank 110 , the second ultrasonic soaking tank 120 and the third ultrasonic soaking tank 130 are all: power 3kw, time 8min, frequency 120kHz.
[0070] S220 , cleaning the soaked and cleaned mask with ultrasonic vibration using the organic cleaning agent.
[0071] Specifically, the soaked and cleaned mask plates are sequentially put into the first ultrasonic ...
Embodiment 3
[0078] A method for cleaning a mask plate, the mask plate being a metal mask plate, the cleaning method comprising the following steps:
[0079] S310, putting the mask plate to be cleaned into an organic cleaning agent for ultrasonic immersion cleaning.
[0080] Specifically, the mask plate to be cleaned is sequentially put into the first ultrasonic soaking tank 110, the second ultrasonic soaking tank 120 and the third ultrasonic soaking tank 130 all filled with the organic cleaning agent, and ultrasonic soaking is carried out. cleaning. The ultrasonic soaking and cleaning conditions of the first ultrasonic soaking tank 110 , the second ultrasonic soaking tank 120 and the third ultrasonic soaking tank 130 are all: the power is 3kw, the time is 8min, and the frequency is 170kHz.
[0081] S320 , cleaning the soaked and cleaned mask with ultrasonic vibration using the organic cleaning agent.
[0082] Specifically, the soaked and cleaned mask plates are sequentially put into the...
PUM
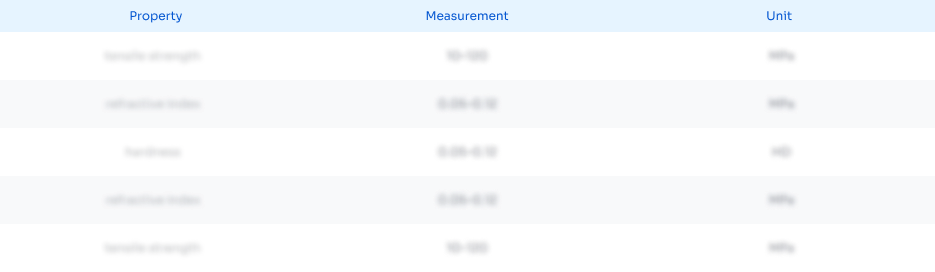
Abstract
Description
Claims
Application Information

- Generate Ideas
- Intellectual Property
- Life Sciences
- Materials
- Tech Scout
- Unparalleled Data Quality
- Higher Quality Content
- 60% Fewer Hallucinations
Browse by: Latest US Patents, China's latest patents, Technical Efficacy Thesaurus, Application Domain, Technology Topic, Popular Technical Reports.
© 2025 PatSnap. All rights reserved.Legal|Privacy policy|Modern Slavery Act Transparency Statement|Sitemap|About US| Contact US: help@patsnap.com