Hexamethylenediamine production system
A production system, the technology of hexamethylenediamine, applied in the chemical industry, can solve the problems of difficult to meet the production of high-quality hexamethylenediamine, unfavorable reaction temperature, difficult heat discharge, etc., and achieve the effect of uniform heat production, uniform reaction and small flow
- Summary
- Abstract
- Description
- Claims
- Application Information
AI Technical Summary
Problems solved by technology
Method used
Image
Examples
Embodiment 1
[0027] see figure 1 , the production system of hexamethylenediamine includes hydrogenation reactor 1, gas-liquid separator 2, the number of hydrogenation reactor 1, gas-liquid separator 2 is the same, and the number of gas-liquid separator 2, hydrogenation reactor 1 is at least In this embodiment, the number of hydrogenation reactors and gas-liquid separators is three, and the hydrogenation reactor at the high position is the first hydrogenation reactor, which is at the left side, and the hydrogenation reaction at the low position The third hydrogenation reactor is located on the right, and the middle hydrogenation reactor is the second hydrogenation reactor, located between the first hydrogenation reactor and the third hydrogenation reactor. The hydrogenation reactor 1 is a gas-liquid-solid three-phase fixed-bed reactor. Specifically, the shell of each hydrogenation reactor is composed of an upper cylindrical section 1a and a lower inverted conical section 1b to form a whole....
Embodiment 2
[0029] The average particle size of the Raney nickel catalyst filled in each hydrogenation reactor was 40 μm. The prepared ethanol solution and sodium hydroxide mixture flowed through three hydrogenation reactors in series in sequence, and the temperature of each hydrogenation reactor was controlled at 73, 75 and 77° C. respectively. Add adiponitrile from the top to the first hydrogenation reactor, the second hydrogenation reactor, and the third hydrogenation reactor, and the total amount of addition is controlled at about 4.5m 3 / h. After the mixed liquid enters the first hydrogenation reactor, it overflows to the second hydrogenation reactor and the third hydrogenation reactor sequentially by utilizing the liquid level difference. The reaction of adiponitrile and hydrogen is an exothermic reaction, and heat exchange is performed in a closed cycle using heat exchange interlayers, heat exchange coils, medium circulation pumps, and heat exchangers. The circulating hydrogen of ...
Embodiment 3
[0032] The average particle size of the Raney nickel catalyst filled in each hydrogenation reactor was 60 μm. The prepared ethanol solution and sodium hydroxide mixture flowed through three series hydrogenation reactors in sequence, and the temperature of each hydrogenation reactor was controlled at 74, 76 and 78° C. respectively. Add adiponitrile from the top to the first hydrogenation reactor, the second hydrogenation reactor, and the third hydrogenation reactor, and the total amount of addition is controlled at about 6m 3 / h. After the mixed liquid enters the first hydrogenation reactor, it overflows to the second hydrogenation reactor and the third hydrogenation reactor sequentially by utilizing the liquid level difference. The reaction of adiponitrile and hydrogen is an exothermic reaction, and heat exchange is performed in a closed cycle using heat exchange interlayers, heat exchange coils, medium circulation pumps, and heat exchangers. The circulating hydrogen of each...
PUM
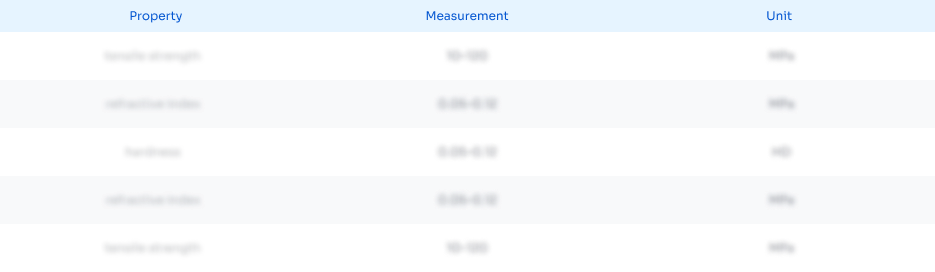
Abstract
Description
Claims
Application Information

- Generate Ideas
- Intellectual Property
- Life Sciences
- Materials
- Tech Scout
- Unparalleled Data Quality
- Higher Quality Content
- 60% Fewer Hallucinations
Browse by: Latest US Patents, China's latest patents, Technical Efficacy Thesaurus, Application Domain, Technology Topic, Popular Technical Reports.
© 2025 PatSnap. All rights reserved.Legal|Privacy policy|Modern Slavery Act Transparency Statement|Sitemap|About US| Contact US: help@patsnap.com