Full-automatic assembly line system for electrostatic powder coating
An electrostatic powder and assembly line technology, applied in the direction of electrostatic spraying device, spraying device, liquid spraying equipment, etc., can solve the problems of poor coating effect, single function, increased workload, etc., achieve flexible position changes, expand the spraying area, reduce The effect of powder waste
- Summary
- Abstract
- Description
- Claims
- Application Information
AI Technical Summary
Problems solved by technology
Method used
Image
Examples
Embodiment Construction
[0024] In order to enable those in the technical field to better understand the solutions of the present invention, the technical solutions in the embodiments of the present invention will be clearly and completely described below in conjunction with the drawings in the embodiments of the present invention.
[0025] Such as Figure 1-15As shown, a fully automatic assembly line system for electrostatic powder coating, including a fixed base 1, a non-contact powder bin 2, a powder recovery system 3, a cylindrical coating bin 4, a suspension conveying structure, a first-stage powder spraying structure 6, two Level powder spraying structure 7 and leveling mechanism 8; the non-contact powder bin 2 is set inside the fixed base 1; the powder recovery system 3 is set in the non-contact powder bin 2; the cylindrical coating The bin 4 is fixedly connected to the fixed base 1; the suspension conveying mechanism 5 is arranged inside the cylindrical coating bin 4; the primary powder sprayi...
PUM
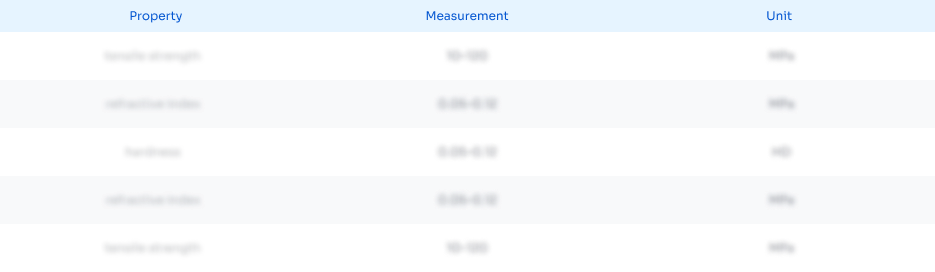
Abstract
Description
Claims
Application Information

- Generate Ideas
- Intellectual Property
- Life Sciences
- Materials
- Tech Scout
- Unparalleled Data Quality
- Higher Quality Content
- 60% Fewer Hallucinations
Browse by: Latest US Patents, China's latest patents, Technical Efficacy Thesaurus, Application Domain, Technology Topic, Popular Technical Reports.
© 2025 PatSnap. All rights reserved.Legal|Privacy policy|Modern Slavery Act Transparency Statement|Sitemap|About US| Contact US: help@patsnap.com