Bearing fault intelligent diagnosis method based on compressed sensing and correlation vector machine
A correlation vector machine and compressed sensing technology, applied in the field of intelligent diagnosis of bearing faults, can solve the problems of low signal-to-noise ratio of bearing vibration signals, difficulties in massive data transmission and processing, etc., to reduce the consumption of transmission resources and computing resources, and improve engineering value and application prospects, the effect of good sparsity
- Summary
- Abstract
- Description
- Claims
- Application Information
AI Technical Summary
Problems solved by technology
Method used
Image
Examples
specific Embodiment
[0084] In this embodiment, the bearing test bench is connected with a data acquisition instrument to collect vibration signals of bearings in different working states. During the experiment, the sampling frequency is set to 15360Hz, the number of sampling points is 8192, and the motor speed n=1496r / min. Bearing parameters are as follows: outer diameter D=80mm, inner diameter d=35mm, number of rolling elements Z=8, contact angle α=0°. In the pitting test of the bearing, the pitting on each component of the bearing is a single point pitting, and the pitting defects are small pits with a diameter of 2mm and a depth of 0.1mm. The process of fault intelligent identification using the correlation vector machine model is as follows:
[0085] (1) First, install the acceleration sensor in the vertical direction of the bearing seat to collect the mechanical vibration signal of the bearing x N×1 , where N is the number of sampling points.
[0086] (2) Selecting a measurement matrix to...
PUM
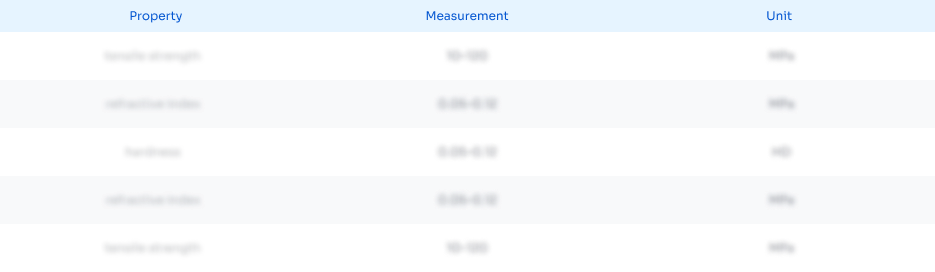
Abstract
Description
Claims
Application Information

- R&D Engineer
- R&D Manager
- IP Professional
- Industry Leading Data Capabilities
- Powerful AI technology
- Patent DNA Extraction
Browse by: Latest US Patents, China's latest patents, Technical Efficacy Thesaurus, Application Domain, Technology Topic, Popular Technical Reports.
© 2024 PatSnap. All rights reserved.Legal|Privacy policy|Modern Slavery Act Transparency Statement|Sitemap|About US| Contact US: help@patsnap.com