Dyeing and finishing process of superfine fiber fabric capable of quickly wicking sweat
A microfiber and fabric technology, applied in the field of elastic fabrics, can solve the problems of weakened water absorption and quick-drying effects, and achieve the effects of making up for poor color fastness, reducing floor space, and maintaining slack
- Summary
- Abstract
- Description
- Claims
- Application Information
AI Technical Summary
Problems solved by technology
Method used
Examples
Embodiment 1
[0023] A dyeing and finishing process for microfiber fabrics, comprising the following steps:
[0024] S1 weaving process: the microfiber fabric is woven into a single-sided weft-knitted plain weave structure through a loom;
[0025] S2 pre-shaping: Pre-shaping the cleaned superfine fiber fabric, the setting temperature is 150°C, and the setting cloth speed is 12m / min;
[0026] S3 pre-treatment: immerse the pre-shaped superfine fiber fabric in hot water at 30°C, add refined degreasing agent Dyamul SORnew, penetrating agent JFC, heat it up to 80°C, keep it warm for 10 minutes, then wash it with water and cool it down to 20°C, and wait for dyeing ;
[0027] S4 Dyeing: Put the superfine fiber fabric in a relaxed state for 5 hours, send it to the overflow dyeing machine, add 2g / L dye and 0.4g / L acid leveling agent for dyeing, and increase the temperature in the dyeing machine at 2°C / min Keep the temperature at 85°C for 3 minutes, then raise the temperature at 1°C / min to 90°C and...
Embodiment 2
[0032] S1 weaving process: the microfiber fabric is woven into a single-sided weft-knitted plain weave structure through a loom;
[0033] S2 pre-shaping: Pre-shaping the cleaned superfine fiber fabric, the setting temperature is 155°C, and the setting cloth speed is 12-15m / min;
[0034] S3 pre-treatment: immerse the pre-shaped superfine fiber fabric in hot water at 32°C, add refined degreasing agent Dyamul SORnew, penetrating agent JFC, heat it up to 80°C, keep it warm for 13 minutes, then wash it with water and cool it down to 22°C, and wait for dyeing ;
[0035] S4 Dyeing: Put the superfine fiber fabric in a relaxed state for 6 hours, send it to the overflow dyeing machine, add 2g / L dye and 0.5g / L acid leveling agent for dyeing, and increase the temperature in the dyeing machine at 2°C / min Keep the temperature at 85°C for 3 minutes, then raise the temperature at 1°C / min to 90°C and keep it for 5 minutes, then raise the temperature at 1.5°C / min to 110°C and keep it for 30 mi...
Embodiment 3
[0040] S1 weaving process: the microfiber fabric is woven into a single-sided weft-knitted plain weave structure through a loom;
[0041] S2 pre-shaping: Pre-shaping the cleaned superfine fiber fabric, the setting temperature is 165°C, and the setting cloth speed is 13m / min;
[0042] S3 pre-treatment: immerse the pre-shaped microfiber fabric in hot water at 30-40°C, add refined degreasing agent Dyamul SORnew, penetrating agent JFC, heat up to 80°C, keep it warm for 15 minutes, then wash with water and cool down to 22.5°C, to be dyed;
[0043]S4 Dyeing: Put the microfiber fabric in a relaxed state for 6.5 hours, send it to the overflow dyeing machine, add 2.5g / L dye and 0.6g / L acid leveling agent for dyeing, and raise the dyeing machine at 2°C / min Keep the temperature at 85°C for 3 minutes, then raise the temperature at 1°C / min to 90°C and keep it for 5 minutes, then raise the temperature at 1.5°C / min to 110°C and keep it for 30 minutes, and finally cool down to 50°C at 1.5°C / ...
PUM
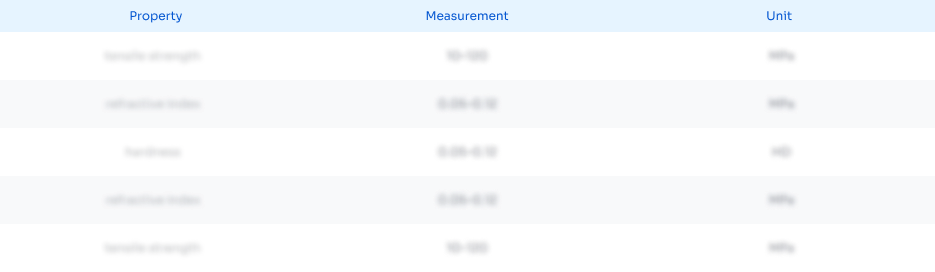
Abstract
Description
Claims
Application Information

- R&D Engineer
- R&D Manager
- IP Professional
- Industry Leading Data Capabilities
- Powerful AI technology
- Patent DNA Extraction
Browse by: Latest US Patents, China's latest patents, Technical Efficacy Thesaurus, Application Domain, Technology Topic, Popular Technical Reports.
© 2024 PatSnap. All rights reserved.Legal|Privacy policy|Modern Slavery Act Transparency Statement|Sitemap|About US| Contact US: help@patsnap.com