Assembling system
An assembly system and tooling technology, applied in assembly machines, metal processing equipment, manufacturing tools, etc., can solve the problems of production line development and manufacturing, high labor costs, high requirements for plant layout and staffing, and low production efficiency. Achieve the effects of improving docking efficiency, reducing development costs, and reducing docking difficulty
- Summary
- Abstract
- Description
- Claims
- Application Information
AI Technical Summary
Problems solved by technology
Method used
Image
Examples
Embodiment 1
[0058] Such as figure 1 As shown, a first embodiment of the present invention provides an assembly system 10 . The assembly system 10 includes a loading tool 500 and a clamping tool 100 .
[0059] Among them, such as figure 1 and Figure 7 As shown, the loading tool 500 includes: a frame 550; at least one clamping mechanism 700, at least one clamping mechanism 700 is arranged on the frame 550, and the clamping mechanism 700 includes: a clamping part 710, a translation part 711 and a lifting part 720, the clamping part 710 is arranged on the translation part 711, the translation part 711 is connected with the jacking part 720, the clamping part 710 is used to clamp the first workpiece 502, and the jacking part 720 is configured to lift the translation part 711 , the translation part 711 can slide relative to the frame 550 in the state of being lifted by the jacking part 720; the transmission mechanism, the transmission mechanism is arranged on the frame, and the transmission...
Embodiment 2
[0064] Such as figure 1 and figure 2 As shown, a second embodiment of the present invention provides an assembly system 10 . The assembly system 10 includes a loading tool 500 and a clamping tool 100 . Among them, such as figure 1 As shown, the loading tool 500 is used for clamping the first workpiece 502 , the clamping tool 100 is used for clamping the second workpiece 102 , and the loading tool 500 is set opposite to the clamping tool 100 . Such as figure 2 As shown, the clamping tool 100 includes a support 200, a positioning mechanism 300 and a turning mechanism 400. The positioning mechanism 300 is rotatably arranged on the support 200. The positioning mechanism 300 is used to clamp the second workpiece 102. The turning mechanism 400 and the positioning The mechanism 300 is connected, and the turning mechanism 400 is configured to be able to drive the positioning mechanism 300 to rotate to adjust the relative position of the first workpiece 502 and the second workpie...
Embodiment 3
[0072] Such as Figure 3 to Figure 5 As shown, on the basis of any of the above embodiments, further, the first positioning assembly 322 includes a first motor 3222 , a first transmission member 3224 and a first positioning block 3226 . The second positioning assembly 324 includes a second motor 3242 , a second transmission member 3244 and a second positioning block 3246 .
[0073]Specifically, the output end of the first motor 3222 is connected to the first transmission member 3224, the first positioning block 3226 is connected to the output end of the first transmission member 3224, and the first motor 3222 can drive the first positioning block 3226 on the positioning surface. The first positioning block 3226 can be fixed in a plurality of preset positions, and the movable first positioning block 3226 can adjust the loading position of the workpiece according to the size of the workpiece, and can meet the needs of different workpieces. The clamping requirements improve the ...
PUM
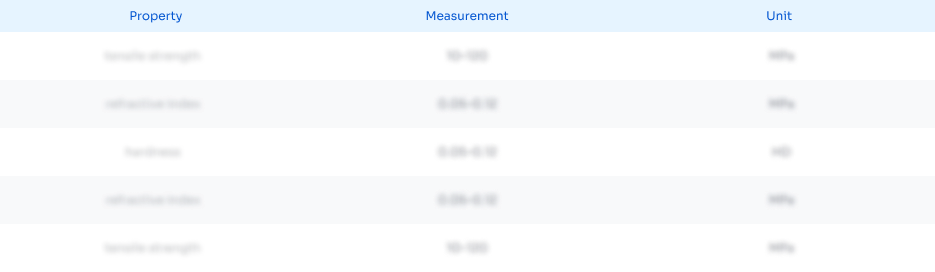
Abstract
Description
Claims
Application Information

- R&D Engineer
- R&D Manager
- IP Professional
- Industry Leading Data Capabilities
- Powerful AI technology
- Patent DNA Extraction
Browse by: Latest US Patents, China's latest patents, Technical Efficacy Thesaurus, Application Domain, Technology Topic, Popular Technical Reports.
© 2024 PatSnap. All rights reserved.Legal|Privacy policy|Modern Slavery Act Transparency Statement|Sitemap|About US| Contact US: help@patsnap.com