Wool processing device for textile industry
A processing device and technology in the textile industry, applied in the direction of cleaning with toothed tools, washing/scouring of loose animal wool fibers, fiber cleaning machines, etc., can solve the problems affecting the research work, the quality of washing wool cannot be guaranteed, and the cleaning effect Poor and other problems to achieve the effect of avoiding stuck
- Summary
- Abstract
- Description
- Claims
- Application Information
AI Technical Summary
Problems solved by technology
Method used
Image
Examples
Embodiment 1
[0027] see Figure 1-3 , in an embodiment of the present invention, a wool processing device for the textile industry, comprising a material transfer box 1, a support column 3 and a cleaning box 4, the support column 3 is fixedly installed on the material transfer box 1, and the material transfer box 1 It is fixedly installed between the cleaning box 4, and the feeding box 1 is provided with a feed port 2. Since the existing wool is glued into a ball when it is harvested from the sheep body, it is not easy to clean and arrange in the later stage. , in order to make the wool loose, a loosening mechanism is provided in the material transfer box 1, and the loosening mechanism includes two groups of first conveyor belts 5 and second conveyor belts 6, and the first conveyor belts 5 and the second conveyor belts 6 are rotatably installed In the material transfer box 1, the first conveyor belt 5 is longitudinally symmetrically arranged on both sides of the second conveyor belt 6, the...
Embodiment 2
[0030] see Figure 4-6, this embodiment makes a further improvement on the basis of embodiment 1, and the improvement content is that a cleaning mechanism is provided in the cleaning box 4 for cleaning the loosened wool, and the cleaning mechanism includes a floating plate 20 and a bottom plate 26, the floating plate 20 is evenly provided with filter holes 21, hinged between the floating plate 20 and the bottom plate 26, the floating plate 20 is provided with a raised portion 14, the raised portion 14 One end is fixedly mounted with a conflict block 19, and one side of the bottom plate 26 is fixedly mounted with a reset lever 25, and the reset lever 25 is connected with a reset plate 24 through an elastic member, and the elastic member can be a spring, a shrapnel, etc. To be specifically defined, a cam 18 is rotatably installed in the cleaning box 4, and a stepper motor 17 for driving the cam 18 is fixedly installed on the cleaning box 4, and the cam 18 interferes with the mov...
Embodiment 1
[0032] In conjunction with embodiment 1, embodiment 2, working principle of the present invention is:
[0033] When using the present invention, the wool balls that are harvested are poured on the second conveyer belt 6 in the material transfer box 1 through the feed port 2, and under the action of the delivery plate 7, the comb plate 9 and the comb point 10, the volume Larger wool balls are loosened, and the work of wool loosening is realized step by step, avoiding the phenomenon of being stuck, and through the action of the main fan 11 and the auxiliary fan 12, the wool on the comb plate 9 and the comb point 10 Blow into the second conveyor belt 6 again, and by the effect of the baffle plate 13, avoid the phenomenon that the wool on the comb point 10 is blown by the main fan 11 and the auxiliary fan 12 and fly randomly in the material transfer box 1, and the wool will be blown to the cleaning box 4, water is injected into the interior, under the action of buoyancy, the float...
PUM
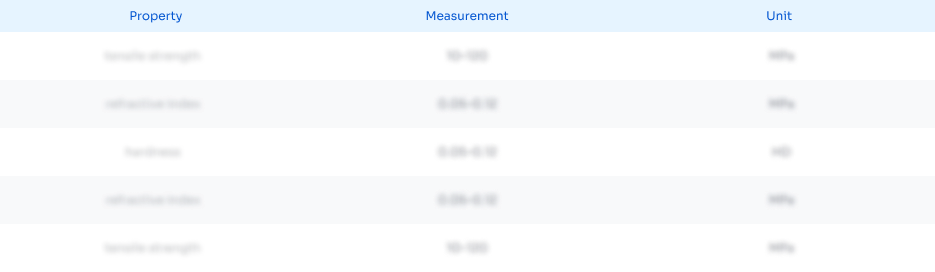
Abstract
Description
Claims
Application Information

- R&D
- Intellectual Property
- Life Sciences
- Materials
- Tech Scout
- Unparalleled Data Quality
- Higher Quality Content
- 60% Fewer Hallucinations
Browse by: Latest US Patents, China's latest patents, Technical Efficacy Thesaurus, Application Domain, Technology Topic, Popular Technical Reports.
© 2025 PatSnap. All rights reserved.Legal|Privacy policy|Modern Slavery Act Transparency Statement|Sitemap|About US| Contact US: help@patsnap.com