Waste heat recovery device and hot rolling production line
A waste heat recovery device and waste heat technology, applied in the field of metallurgy, can solve problems such as heat loss, heat loss, and energy waste
- Summary
- Abstract
- Description
- Claims
- Application Information
AI Technical Summary
Problems solved by technology
Method used
Image
Examples
Embodiment 1
[0038] The embodiment provides a waste heat recovery device, which can be used in the production of hot-rolled steel, and can recover the waste heat of the hot-rolled steel 9 itself, so as to achieve the effect of energy recovery and energy saving, so as to solve the problem of hot-rolled steel production process. problem of energy waste.
[0039] Such as figure 1 and figure 2 As shown, the waste heat recovery device includes a heat exchange chamber 1 . The end of the heat exchange chamber 1 is provided with a material delivery port 12 so that materials can enter and leave the heat exchange chamber 1 through the material delivery port 12 . Wherein, the material may be hot-rolled steel 9; specifically, the material may be a hot-rolled stainless steel coil after hot-rolling. The hot-rolled steel 9 can exchange heat with the gas in the heat exchange chamber 1 to form heat energy gas.
[0040] Certainly, in some other embodiments, the hot-rolled steel 9 may also be hot-rolled...
Embodiment 2
[0046] The embodiment provides a waste heat recovery device, it can be understood that this embodiment is a further improvement on the basis of the first embodiment.
[0047] Such as figure 1 and figure 2 As shown, the heat exchange chamber 1 includes a shell 11, and the inside of the shell 11 is the space for heat exchange between the hot-rolled steel 9 and the low-temperature gas.
[0048] In some embodiments, the casing 11 may include a steel shell and an insulating material filled inside the steel shell. Therefore, the heat insulation effect of the housing 11 is realized, and the heat inside the housing 11 is guaranteed not to be dissipated outward, that is, the heat exchange chamber 1 is insulated from the external environment, and the waste heat recovery rate is improved.
[0049] Exemplarily, the insulation material filled inside the housing 11 can be selected from materials such as polyurethane foam, glass wool, foamed cement, and rock wool.
[0050] In an embodime...
Embodiment 3
[0089] The embodiment also provides a hot rolling production line, including the waste heat recovery device provided in the first or second embodiment.
[0090] Wherein, the hot rolling production line may also include sequentially setting a heating furnace, a hot rolling mechanism and a coiler. The strip steel heated by the heating furnace is transported to the hot rolling mechanism for hot rolling, and then sent to the coiler to be coiled into steel coils. The hot-rolled steel 9 after being coiled can be sent to the waste heat recovery device for waste heat recovery, and the hot-rolled steel 9 itself is cooled down. The cooled hot rolled steel 9 can be transferred to the finished product bay for storage.
PUM
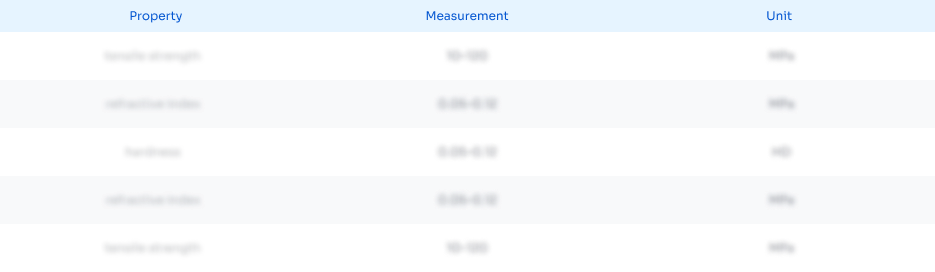
Abstract
Description
Claims
Application Information

- R&D Engineer
- R&D Manager
- IP Professional
- Industry Leading Data Capabilities
- Powerful AI technology
- Patent DNA Extraction
Browse by: Latest US Patents, China's latest patents, Technical Efficacy Thesaurus, Application Domain, Technology Topic, Popular Technical Reports.
© 2024 PatSnap. All rights reserved.Legal|Privacy policy|Modern Slavery Act Transparency Statement|Sitemap|About US| Contact US: help@patsnap.com