A Second Tool Setting Method for 3+2 Axis Machine Tool Machining
A technology of secondary tool setting and machine tool, applied in metal processing, metal processing equipment, metal processing mechanical parts, etc., can solve the problems of no re-confirmation and difficult tool setting for secondary tool setting, etc.
- Summary
- Abstract
- Description
- Claims
- Application Information
AI Technical Summary
Problems solved by technology
Method used
Image
Examples
Embodiment 2
[0072] The difference between embodiment two and embodiment one is:
[0073] The 3+2-axis machine tool includes a support frame (not shown in the figure), the support frame is fixedly connected to the working platform 1, and the working platform 1 is embedded with a pusher, the pusher is the push cylinder 7, and the push cylinder 7 is completely accommodated and In the working platform 1, the protruding end of the pushing cylinder 7 is set perpendicular to the supporting surface of the working platform 1 toward the machine head 6, and the protruding end of the pushing cylinder 7 is fixedly connected with a reference gauge block 8, which is set in a cube. The three adjacent edges of any top angle of the gauge block 8 are respectively parallel to the length direction of the X-axis driving part 3, the Y-axis driving part 4 and the Z-axis driving part 5 of the machine tool. The supporting surface of the working platform 1 There is a storage slot 2 for inserting the reference gauge...
PUM
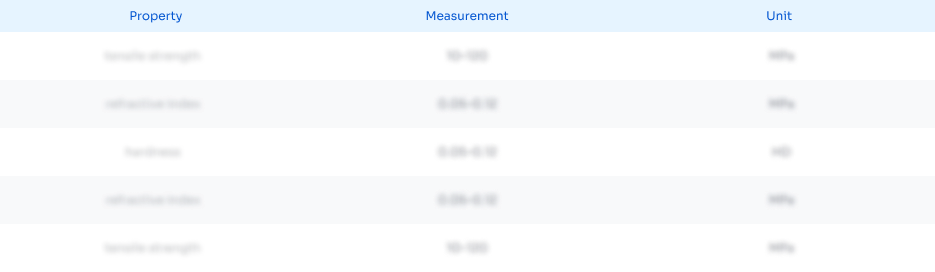
Abstract
Description
Claims
Application Information

- R&D
- Intellectual Property
- Life Sciences
- Materials
- Tech Scout
- Unparalleled Data Quality
- Higher Quality Content
- 60% Fewer Hallucinations
Browse by: Latest US Patents, China's latest patents, Technical Efficacy Thesaurus, Application Domain, Technology Topic, Popular Technical Reports.
© 2025 PatSnap. All rights reserved.Legal|Privacy policy|Modern Slavery Act Transparency Statement|Sitemap|About US| Contact US: help@patsnap.com