Energy consumption optimal trajectory planning method for welding robot
A welding robot and trajectory planning technology, applied in welding equipment, auxiliary welding equipment, welding/cutting auxiliary equipment, etc., can solve the problem of inability to solve the uncertainty of jumping between multiple points and the optimal energy consumption between multiple points And other issues
- Summary
- Abstract
- Description
- Claims
- Application Information
AI Technical Summary
Problems solved by technology
Method used
Image
Examples
Embodiment Construction
[0040] The technical solutions of the present invention will be clearly and completely described below in conjunction with the accompanying drawings. Apparently, the described embodiments are some of the embodiments of the present invention, but not all of them. Based on the embodiments of the present invention, all other embodiments obtained by persons of ordinary skill in the art without making creative efforts belong to the protection scope of the present invention.
[0041] The invention discloses a trajectory planning method for optimal energy consumption of a welding robot, comprising the following steps:
[0042] Step S1) first transform the welding points in the working space of the welding robot into a point cloud in Cartesian space; transform the robot welding trajectory into a point cloud sequence;
[0043] Step S2) Use the quintic polynomial interpolation in the joint space of the robot to uniformly plan the jump trajectory between any two points in the point cloud...
PUM
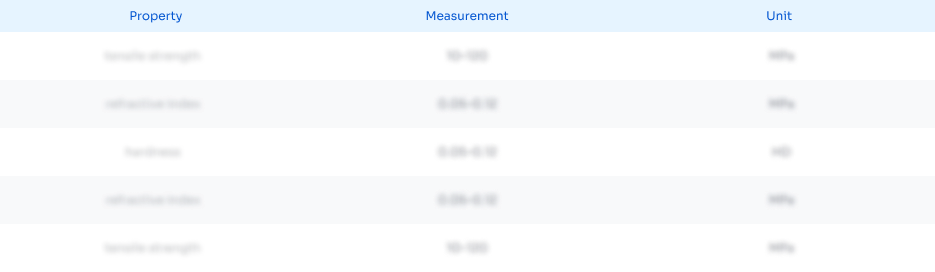
Abstract
Description
Claims
Application Information

- R&D
- Intellectual Property
- Life Sciences
- Materials
- Tech Scout
- Unparalleled Data Quality
- Higher Quality Content
- 60% Fewer Hallucinations
Browse by: Latest US Patents, China's latest patents, Technical Efficacy Thesaurus, Application Domain, Technology Topic, Popular Technical Reports.
© 2025 PatSnap. All rights reserved.Legal|Privacy policy|Modern Slavery Act Transparency Statement|Sitemap|About US| Contact US: help@patsnap.com