A method for treating the base of a corrosion-resistant steel silo
A treatment method and steel silo technology, applied to pretreatment surfaces, primers, anti-corrosion coatings, etc., can solve problems such as surface corrosion, internal storage items corruption, and damage to the storage environment of steel silos, so as to improve the service life and prevent Damage, the effect of improving the binding force
- Summary
- Abstract
- Description
- Claims
- Application Information
AI Technical Summary
Problems solved by technology
Method used
Image
Examples
Embodiment 1
[0075] A method for treating the base of a corrosion-resistant steel silo, comprising the following steps:
[0076] (1) Cleaning and polishing:
[0077] The base of the steel silo was cleaned with acetone to remove surface oil, and then cleaned with an ethanol solution with a mass fraction of 30%. After drying, it was polished with sandpaper of different meshes to obtain a polished steel silo base; The grinding with sandpaper of different mesh numbers is to use 300 mesh, 600 mesh and 1200 mesh sandpaper to polish successively; wherein, the 300 mesh sandpaper is polished for 20 minutes; the 600 mesh sandpaper is polished for 35 minutes; the 1200 mesh sandpaper is polished for 1 hour.
[0078] (2) Steel silo base pretreatment:
[0079] Preparation of pretreatment solution: add silane coupling agent, maleic anhydride, strontium chloride, absolute ethanol, and deionized water to the reaction kettle in sequence, heat to 50°C, and stir for 30 minutes to obtain the pretreatment solu...
Embodiment 2
[0087] A method for treating the base of a corrosion-resistant steel silo, comprising the following steps:
[0088] (1) Cleaning and polishing:
[0089] The base of the steel silo was cleaned with acetone to remove surface oil, and then cleaned with an ethanol solution with a mass fraction of 30%. After drying, it was polished with sandpaper of different meshes to obtain a polished steel silo base; The grinding with sandpaper of different mesh numbers is to use 300 mesh, 600 mesh and 1200 mesh sandpaper to polish successively; wherein, the 300 mesh sandpaper is polished for 20 minutes; the 600 mesh sandpaper is polished for 35 minutes; the 1200 mesh sandpaper is polished for 1 hour.
[0090] (2) Steel silo base pretreatment:
[0091] Preparation of pretreatment solution: add silane coupling agent, maleic anhydride, strontium chloride, absolute ethanol, and deionized water to the reaction kettle in sequence, heat to 50°C, and stir for 30 minutes to obtain the pretreatment solu...
Embodiment 3
[0099] A method for treating the base of a corrosion-resistant steel silo, comprising the following steps:
[0100] (1) Cleaning and polishing:
[0101] The base of the steel silo was cleaned with acetone to remove surface oil, and then cleaned with an ethanol solution with a mass fraction of 30%. After drying, it was polished with sandpaper of different meshes to obtain a polished steel silo base; The grinding with sandpaper of different mesh numbers is to use 300 mesh, 600 mesh and 1200 mesh sandpaper to polish successively; wherein, the 300 mesh sandpaper is polished for 20 minutes; the 600 mesh sandpaper is polished for 35 minutes; the 1200 mesh sandpaper is polished for 1 hour.
[0102] (2) Steel silo base pretreatment:
[0103] Preparation of pretreatment solution: add silane coupling agent, maleic anhydride, strontium chloride, absolute ethanol, and deionized water to the reaction kettle in sequence, heat to 50°C, and stir for 30 minutes to obtain the pretreatment solu...
PUM
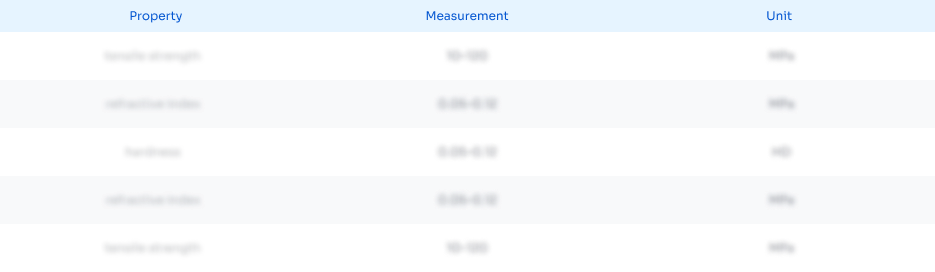
Abstract
Description
Claims
Application Information

- Generate Ideas
- Intellectual Property
- Life Sciences
- Materials
- Tech Scout
- Unparalleled Data Quality
- Higher Quality Content
- 60% Fewer Hallucinations
Browse by: Latest US Patents, China's latest patents, Technical Efficacy Thesaurus, Application Domain, Technology Topic, Popular Technical Reports.
© 2025 PatSnap. All rights reserved.Legal|Privacy policy|Modern Slavery Act Transparency Statement|Sitemap|About US| Contact US: help@patsnap.com