A method for simultaneous desulfurization and denitrification by ozone fractional oxidation combined with wet absorption
A graded oxidation, desulfurization and denitrification technology, applied in the field of flue gas desulfurization and denitrification treatment, can solve the problems of high investment and operation costs, difficulty in meeting emission standards, and secondary impact on the environment, so as to save investment and operation costs and low comprehensive economic cost , Reduce the effect of ozone input
- Summary
- Abstract
- Description
- Claims
- Application Information
AI Technical Summary
Problems solved by technology
Method used
Image
Examples
specific Embodiment 1
[0047] NO x Low initial concentration (less than 200mg / m 3 ), high emission standards (higher than 140mg / m 3 ). Apply technical route 1 as above. Control O 3 / NO molar ratio is around 1.0, ozone initially oxidizes NO x , to ensure a reaction time of at least 0.2s, and to ensure that the flue gas temperature range of the ozone oxidation reaction is 60°C; to oxidize NO in the flue gas to NO 2 , and then pass the oxidized flue gas into the 3 / CaO conventional desulfurization slurry synergistically absorbs SO 2 and NO 2 Gas; in the wet scrubber, the liquid-to-gas ratio is 8L / m 3 , the number of spray tower layers is 2, and the residence time of the flue gas is ≥ 2s; the purified flue gas is discharged from the chimney, and the reacted slurry is processed to produce chemical products such as gypsum and nitrite. Final NO x The removal efficiency is about 30%, SO 2 The removal efficiency is above 90%.
specific Embodiment 2
[0049] NO x Low initial concentration (less than 200mg / m 3 ), high emission standards (higher than 140mg / m 3 ). Apply technical route 1 as above. Control O 3 / NO molar ratio is about 1.1, ozone initially oxidizes NO x , to ensure a reaction time of at least 0.2s, and to ensure that the flue gas temperature range of the ozone oxidation reaction is 130°C; to oxidize NO in the flue gas to NO 2 , and then pass the oxidized flue gas into the 3 / CaO conventional desulfurization slurry synergistically absorbs SO 2 and NO 2 Gas; in the wet scrubber, the liquid-to-gas ratio is 12L / m 3 , the number of spray tower layers is 3, and the residence time of the flue gas is ≥ 2s; the purified flue gas is discharged from the chimney, and the reacted slurry is processed to produce chemical products such as gypsum and nitrite. Final NO x The removal efficiency is about 30%, SO 2 The removal efficiency is above 90%.
specific Embodiment 3
[0051] NO x Low initial concentration (less than 200mg / m 3 ), high emission standards (higher than 140mg / m 3 ). Apply technical route 1 as above. Control O 3 The / NO molar ratio is about 1.2, and the ozone initially oxidizes NO x , to ensure a reaction time of at least 0.2s, and to ensure that the flue gas temperature range of the ozone oxidation reaction is 180°C; to oxidize NO in the flue gas to NO 2 , and then pass the oxidized flue gas into the 3 / CaO conventional desulfurization slurry synergistically absorbs SO 2 and NO 2 Gas; in the wet scrubber, the liquid-to-gas ratio is 16L / m 3 , the number of spray tower layers is 4, and the residence time of the flue gas is ≥ 2s; the purified flue gas is discharged from the chimney, and the reacted slurry is processed to produce chemical products such as gypsum and nitrite. Final NO x The removal efficiency is about 30%, SO 2 The removal efficiency is above 90%.
PUM
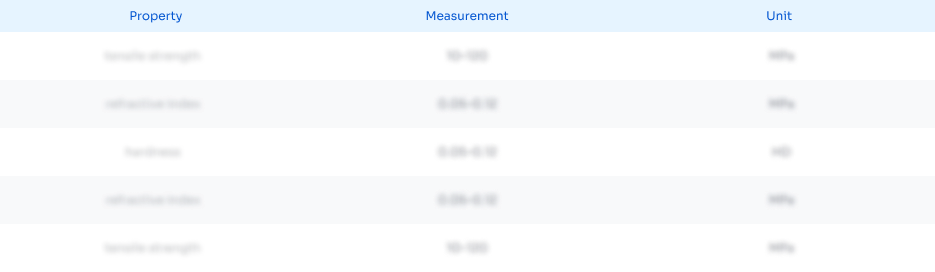
Abstract
Description
Claims
Application Information

- Generate Ideas
- Intellectual Property
- Life Sciences
- Materials
- Tech Scout
- Unparalleled Data Quality
- Higher Quality Content
- 60% Fewer Hallucinations
Browse by: Latest US Patents, China's latest patents, Technical Efficacy Thesaurus, Application Domain, Technology Topic, Popular Technical Reports.
© 2025 PatSnap. All rights reserved.Legal|Privacy policy|Modern Slavery Act Transparency Statement|Sitemap|About US| Contact US: help@patsnap.com