Method for realizing sectional replacement of refractory materials of sleeve kiln and prolonging kiln service life
A sleeve kiln and refractory technology, which is used in furnaces, lining repair, lighting and heating equipment, etc., can solve problems such as destructive demolition, reduce time and cost, reduce refractory costs, and prolong kiln service.
- Summary
- Abstract
- Description
- Claims
- Application Information
AI Technical Summary
Problems solved by technology
Method used
Image
Examples
Embodiment 1
[0025] Embodiment 1: see figure 1 , a method for realizing segmental replacement of sleeve kiln refractory materials and prolonging kiln service, said method comprising the following steps:
[0026] Step 1: The refractory material needs to be replaced and removed in the kiln;
[0027] Step 2: Construction of the bottom structure of the upper inner cylinder;
[0028] Step 3: Construction of the bottom structure of the upper diversion cap;
[0029] Step 4: Improvement of the structure of the lower inner cylinder support brick circle:
[0030] Step 5: Improve construction of the pouring material structure at the bottom of the lower inner tube. At present, the refractory materials in the kiln have been used for about 5 years and cannot be used normally due to the damage of some refractory materials. The existing refractory structure determines that it is impossible to partially dismantle and replace the refractory materials in the kiln. They must be replaced all at once, which ...
PUM
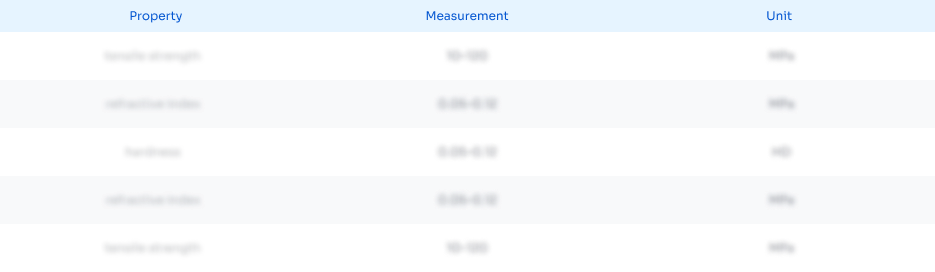
Abstract
Description
Claims
Application Information

- R&D
- Intellectual Property
- Life Sciences
- Materials
- Tech Scout
- Unparalleled Data Quality
- Higher Quality Content
- 60% Fewer Hallucinations
Browse by: Latest US Patents, China's latest patents, Technical Efficacy Thesaurus, Application Domain, Technology Topic, Popular Technical Reports.
© 2025 PatSnap. All rights reserved.Legal|Privacy policy|Modern Slavery Act Transparency Statement|Sitemap|About US| Contact US: help@patsnap.com