Production method for increasing continuous pouring times for calcium-free treatment of cold heading steel in furnace
A production method and calcium treatment technology, applied in the field of metallurgy, can solve problems such as production interruption, and achieve the effect of reducing the risk of large-particle inclusions exceeding the standard and avoiding nozzle nodules
- Summary
- Abstract
- Description
- Claims
- Application Information
AI Technical Summary
Problems solved by technology
Method used
Image
Examples
Embodiment 1
[0023] In the converter smelting process, the dissolved oxygen content in the molten steel at the end of the smelting process is 385ppm. In the converter tapping process, deoxidation and alloying are carried out during the tapping process, so that the Al content in the incoming molten steel composition of the LF furnace is 0.025%, and high alkali is added when tapping 2 / 3 of the converter Pre-melted slag and lime, the amount of pre-melted slag and lime added is 3.5kg / ton of steel, and the binary alkalinity of ladle slag is controlled at 10.0. LF process, add lime 2.5kg / ton of steel when the LF furnace starts heating for 0.5 minutes, control the binary alkalinity of the refining slag to be 13.0 when the LF furnace starts heating; feed aluminum wires to control the aluminum content of molten steel at 0.052 when the LF furnace is treated for 12 minutes %, the aluminum content of the finished molten steel is controlled to be 0.015%, and the feeding time of the aluminum wire ensures...
Embodiment 2
[0025] In the converter smelting process, the dissolved oxygen content in the molten steel at the end of the smelting process is 413ppm. In the converter tapping process, deoxidation and alloying are carried out during the tapping process, so that the Al content in the incoming molten steel composition of the LF furnace is 0.029%, and high alkalinity is added when the converter tapping reaches 70%. Pre-melted slag and lime, the amount of pre-melted slag and lime added is 3.75kg / ton of steel, and the binary basicity of ladle slag is controlled at 9.2. In the LF process, add lime 2.6kg / ton of steel when the LF furnace starts heating for 0.7 minutes, and control the binary alkalinity of the refining slag to be 12.0 when the LF furnace starts heating; feed aluminum wire to control the aluminum content of molten steel at 0.051 when the LF furnace is treated for 5 minutes %, the aluminum content of the finished molten steel is controlled to be 0.024%, and the aluminum wire feeding ti...
Embodiment 3
[0027] In the converter smelting process, the dissolved oxygen content in the molten steel at the end of the smelting process is 345ppm. In the converter tapping process, deoxidation and alloying are carried out during the tapping process, so that the Al content in the incoming molten steel composition of the LF furnace is 0.035%, and high alkalinity is added when the converter tapping is 65%. Pre-melted slag and lime, the amount of pre-melted slag and lime added is 3.65kg / ton of steel respectively, and the binary basicity of ladle slag is controlled at 9.4. In the LF process, add lime 2.7kg / ton of steel when the LF furnace starts heating for 0.9 minutes, and control the binary alkalinity of the refining slag to be 11.0 when the LF furnace starts heating; feed aluminum wires to control the aluminum content of molten steel at 0.053 when the LF furnace starts heating for 11 minutes %, the aluminum content of the finished molten steel is controlled to be 0.023%, and the aluminum w...
PUM
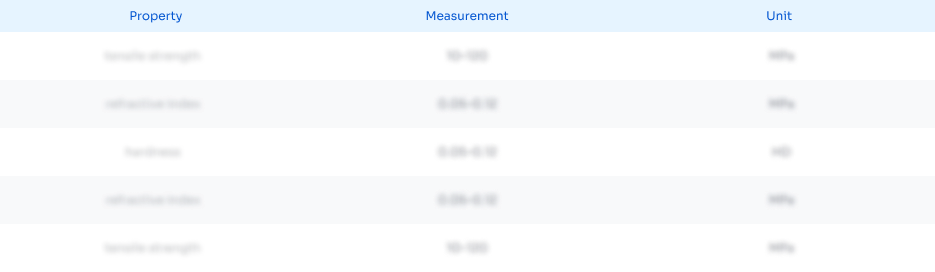
Abstract
Description
Claims
Application Information

- R&D
- Intellectual Property
- Life Sciences
- Materials
- Tech Scout
- Unparalleled Data Quality
- Higher Quality Content
- 60% Fewer Hallucinations
Browse by: Latest US Patents, China's latest patents, Technical Efficacy Thesaurus, Application Domain, Technology Topic, Popular Technical Reports.
© 2025 PatSnap. All rights reserved.Legal|Privacy policy|Modern Slavery Act Transparency Statement|Sitemap|About US| Contact US: help@patsnap.com