Self-flowing heat-resistant concrete utilizing waste electric porcelain
A technology of heat-resistant concrete and electric porcelain, which is applied in the field of materials, can solve problems such as easy bursting, and achieve the effects of good fluidity, low impurity content, and good sintering stability
- Summary
- Abstract
- Description
- Claims
- Application Information
AI Technical Summary
Problems solved by technology
Method used
Image
Examples
Embodiment 1
[0029] Self-flowing refractory concrete aggregate powder consists of the following raw material components and weight percentages:
[0030]
[0031] The physicochemical index of embodiment 1 gained self-flowing heat-resistant concrete is as shown in table 1:
[0032] Table 1
[0033]
[0034]
Embodiment 2
[0036] Self-flowing refractory concrete aggregate powder consists of the following raw material components and weight percentages:
[0037]
[0038] The physicochemical index of embodiment 2 gained self-flowing heat-resistant concrete is as shown in table 2:
[0039] Table 2
[0040]
[0041]
Embodiment 3
[0043] Self-flowing refractory concrete aggregate powder consists of the following raw material components and weight percentages:
[0044]
[0045] The physicochemical index of embodiment 3 gained self-flowing heat-resistant concrete is as shown in table 3:
[0046] table 3
[0047]
PUM
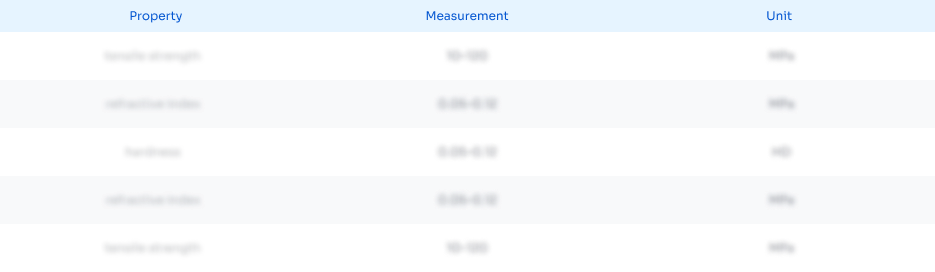
Abstract
Description
Claims
Application Information

- R&D
- Intellectual Property
- Life Sciences
- Materials
- Tech Scout
- Unparalleled Data Quality
- Higher Quality Content
- 60% Fewer Hallucinations
Browse by: Latest US Patents, China's latest patents, Technical Efficacy Thesaurus, Application Domain, Technology Topic, Popular Technical Reports.
© 2025 PatSnap. All rights reserved.Legal|Privacy policy|Modern Slavery Act Transparency Statement|Sitemap|About US| Contact US: help@patsnap.com