Drive control system for elevator permanent magnet synchronous motor
A permanent magnet synchronous motor and drive control technology, applied in motor generator control, control system, electronic commutation motor control, etc. Problems such as the increase of moment observation deviation
- Summary
- Abstract
- Description
- Claims
- Application Information
AI Technical Summary
Problems solved by technology
Method used
Image
Examples
Embodiment 1
[0073] In formula (7), is the observed value of the load torque, is the rotor angular velocity estimate, g is the feedback gain of the load torque observer, k g is the sliding mode gain of the load torque observer embodiment 1, and the load torque observer embodiment 1 is a sliding mode observer. Compared with the load torque, the motor friction has a small proportion, so that B=0, ignoring the influence of friction, then the load torque observer embodiment 1 of formula (7) becomes:
[0074]
[0075] According to (6) and formula (8) when B=0, obtain the error equation of load torque observer embodiment 1 as:
[0076]
[0077] In formula (9), is the rotor angular velocity estimation error, Observing the error for the load torque, and defining the sliding surface of the observer as According to the sliding mode accessibility condition, the stability condition of the observer system in equation (8) is k g ≤-|e 2 / J|, and g<0.
Embodiment 2
[0080] Compared with the load torque, the motor friction has a small proportion, so that B=0, ignoring the influence of friction, then the load torque observer embodiment 2 of formula (10) becomes:
[0081]
[0082] In formula (10), (11), is the observed value of the load torque, is the rotor angular velocity estimate, g is the feedback gain of the load torque observer, k W is the proportional gain of the load torque observer embodiment 2, and the load torque observer embodiment 2 is a state observer. According to the formula (6) and formula (11) when B=0, the error equation of the load torque observer embodiment 2 is obtained as:
[0083]
[0084] In formula (12), is the rotor angular velocity estimation error, is the load torque observation error. The state observer of formula (11) is an autonomous linear system, at k W <0, and g<0, the observer is asymptotically stable. The formula (7) of the load torque observer embodiment 1 and the formula (10) of the l...
PUM
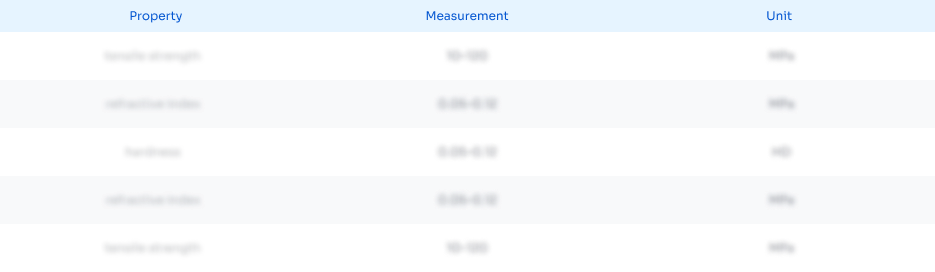
Abstract
Description
Claims
Application Information

- R&D
- Intellectual Property
- Life Sciences
- Materials
- Tech Scout
- Unparalleled Data Quality
- Higher Quality Content
- 60% Fewer Hallucinations
Browse by: Latest US Patents, China's latest patents, Technical Efficacy Thesaurus, Application Domain, Technology Topic, Popular Technical Reports.
© 2025 PatSnap. All rights reserved.Legal|Privacy policy|Modern Slavery Act Transparency Statement|Sitemap|About US| Contact US: help@patsnap.com