Disc brake lubricating system and manufacturing method thereof
A disc brake and lubrication system technology, applied in the direction of brake type, brake parts, engine lubrication, etc., can solve the problems of increased clearance, increased maintenance costs, poor braking performance, etc., to ensure smooth sliding and speed up the solution Effect of wear and aging, high wear resistance
- Summary
- Abstract
- Description
- Claims
- Application Information
AI Technical Summary
Problems solved by technology
Method used
Image
Examples
Embodiment Construction
[0011] The preferred embodiments of the present invention are given below in conjunction with the accompanying drawings to describe the technical solution of the present invention in detail.
[0012] Such as Figure 1 to Figure 3 As shown, the disc brake lubrication system of the present invention includes a bracket 1, a floating inlay 2, a guide pin 3, a block 4, a grease nipple 5, a grease joint 6, a steel cap 7, a bushing 8, a bolt 9, and a spiral groove 10, The floating inlay 2 is located on the top of the bracket 1, the guide pin 3 is located on the side of the bracket 1, the block 4 is located in the guide pin 3, the steel cap 7 is located on one side of the floating inlay 2, the grease joint 6 is connected to the steel cap 7, The oil nozzle 5 communicates with the grease joint 6, the bushing 8 is located between the bracket 1 and the guide pin 3, the bracket 1 and the block 4 are connected by bolts 9, and the spiral groove 10 is located on the outside of the guide pin 3...
PUM
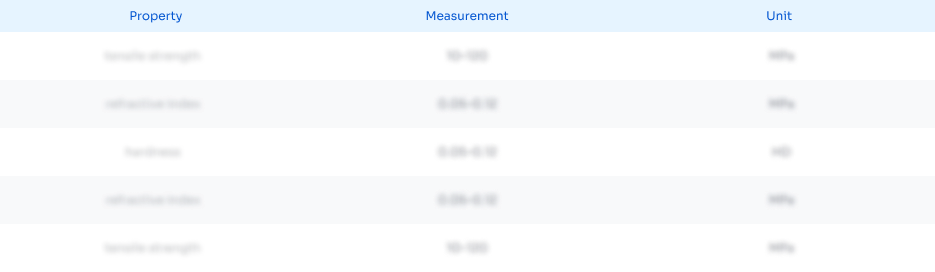
Abstract
Description
Claims
Application Information

- R&D
- Intellectual Property
- Life Sciences
- Materials
- Tech Scout
- Unparalleled Data Quality
- Higher Quality Content
- 60% Fewer Hallucinations
Browse by: Latest US Patents, China's latest patents, Technical Efficacy Thesaurus, Application Domain, Technology Topic, Popular Technical Reports.
© 2025 PatSnap. All rights reserved.Legal|Privacy policy|Modern Slavery Act Transparency Statement|Sitemap|About US| Contact US: help@patsnap.com