Motor position sensorless control method and device
A control method and sensor technology, applied in the current controller and other directions, can solve the problems of not considering the high-frequency variation of the inductance differential term, unable to express the true characteristics of the inductance, motor control divergence, etc., to avoid control divergence and ensure closed-loop control convergence. Effect
- Summary
- Abstract
- Description
- Claims
- Application Information
AI Technical Summary
Problems solved by technology
Method used
Image
Examples
Embodiment Construction
[0039] The technical solutions of the present invention will be further described below with reference to the accompanying drawings.
[0040] see figure 1 , which is a schematic flowchart of a method for controlling a motor without a position sensor provided by the present invention, including specific steps.
[0041] Step 1. Set the initial motor phase current peak value.
[0042] In a specific implementation, usually the initial phase current peak value is smaller than the phase current limit value, in order to leave room for increasing the current step value, the phase current peak value may refer to the three-phase current vector amplitude of the motor.
[0043] Step 2, scan to obtain the orthogonal axis current within the preset current angle range under the peak value of the phase current; determine the orthogonal axis current that satisfies the constraint relationship between the direct axis inductance and the quadrature axis inductance, and set the obtained orthogonal...
PUM
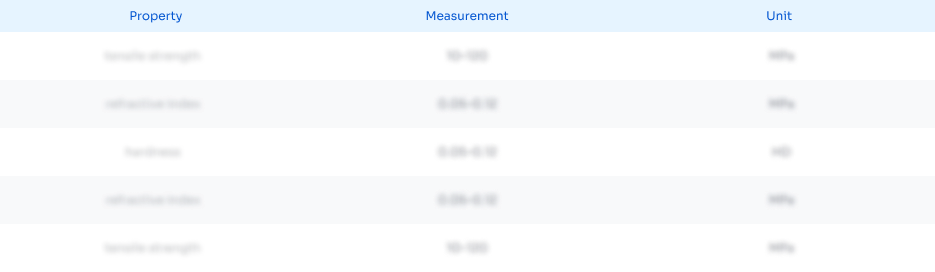
Abstract
Description
Claims
Application Information

- R&D
- Intellectual Property
- Life Sciences
- Materials
- Tech Scout
- Unparalleled Data Quality
- Higher Quality Content
- 60% Fewer Hallucinations
Browse by: Latest US Patents, China's latest patents, Technical Efficacy Thesaurus, Application Domain, Technology Topic, Popular Technical Reports.
© 2025 PatSnap. All rights reserved.Legal|Privacy policy|Modern Slavery Act Transparency Statement|Sitemap|About US| Contact US: help@patsnap.com