Inner hexahedron punching manufacturing method
A manufacturing method and hexahedron technology, applied in the field of punching manufacturing, can solve the problems of semi-finished parts impact, matrix deformation, influence, etc.
- Summary
- Abstract
- Description
- Claims
- Application Information
AI Technical Summary
Problems solved by technology
Method used
Image
Examples
Embodiment Construction
[0068] In order to make the technical means, creative features, goals and effects achieved by the present invention easy to understand, the present invention will be further described below in conjunction with specific illustrations.
[0069] see Figure 1 to Figure 8 The internal hexahedron punching manufacturing method, the specific steps are as follows:
[0070] 1. Determine the technical scheme for reducing the cutting force of the inner hexahedron punching manufacturing method
[0071] Based on the previous machining process, it is determined to increase the diameter of the prefabricated bottom hole to reduce the amount of back cutting during punching. The diameter of the prefabricated bottom hole in the less-cutting manufacturing method is larger than the corresponding side-to-side size of the inner hexahedron, which can be achieved. The amount of back cutting is reduced, and the cutting force is also reduced.
[0072] 2. Establish a less-cutting model of the inner hex...
PUM
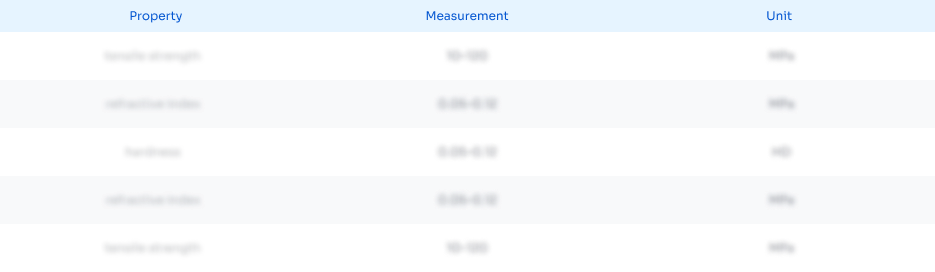
Abstract
Description
Claims
Application Information

- R&D
- Intellectual Property
- Life Sciences
- Materials
- Tech Scout
- Unparalleled Data Quality
- Higher Quality Content
- 60% Fewer Hallucinations
Browse by: Latest US Patents, China's latest patents, Technical Efficacy Thesaurus, Application Domain, Technology Topic, Popular Technical Reports.
© 2025 PatSnap. All rights reserved.Legal|Privacy policy|Modern Slavery Act Transparency Statement|Sitemap|About US| Contact US: help@patsnap.com