Automatic material module testing and packaging system and method
A module testing and packaging system technology, applied in the field of automation, can solve the problems of low efficiency of manual operation, error-prone sorting for a long time, and employee operation errors, and achieves the effect of saving reclaiming time, simple structure and increasing production capacity.
- Summary
- Abstract
- Description
- Claims
- Application Information
AI Technical Summary
Problems solved by technology
Method used
Image
Examples
specific Embodiment approach
[0063] Such as Figure 1-24 As shown, the present invention provides a kind of automatic material module testing packaging system, the main purpose of this testing packaging system is to carry out automatic batch testing and packaging on the assembly line to the circuit module of electronic equipment; A material recovery device A, a feeding device B, a testing device C and a packaging device D arranged along the X-axis direction; a conveying mechanism 25 is connected between the feeding device B and the testing device C, and between the testing device C and the testing device C An output mechanism 40 is connected between the packaging devices D.
[0064] Specifically: if Figure 1-6 As shown, the pallet loading and recycling device A includes a frame 1, and a lower conveying assembly 2 is provided below the frame 1. The front end of the lower conveying assembly 2 has a pallet placement station 3, and a plurality of pallets 4. After stacking, place it on the pallet placement ...
PUM
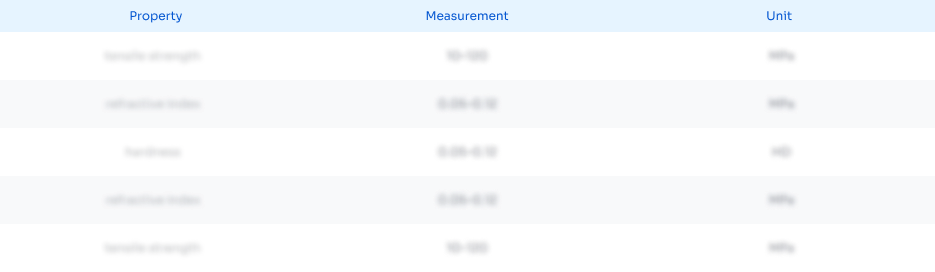
Abstract
Description
Claims
Application Information

- Generate Ideas
- Intellectual Property
- Life Sciences
- Materials
- Tech Scout
- Unparalleled Data Quality
- Higher Quality Content
- 60% Fewer Hallucinations
Browse by: Latest US Patents, China's latest patents, Technical Efficacy Thesaurus, Application Domain, Technology Topic, Popular Technical Reports.
© 2025 PatSnap. All rights reserved.Legal|Privacy policy|Modern Slavery Act Transparency Statement|Sitemap|About US| Contact US: help@patsnap.com