Planetary gear reduction mechanism and steering engine
A technology of planetary gear reduction and deceleration mechanism, which is applied in the direction of gear transmission, belt/chain/gear, electromechanical device, etc., which can solve the problems of uncompact equipment structure, inconvenient maintenance work, scattered and other problems, and achieve regular wiring and reduce space , reduce the effect of resonance
- Summary
- Abstract
- Description
- Claims
- Application Information
AI Technical Summary
Problems solved by technology
Method used
Image
Examples
Embodiment 1
[0053] This embodiment provides a steering gear, such as Figure 8 with Figure 9 As shown, it includes: a planetary gear reduction mechanism and a motor 12, and the motor 12 is connected in transmission with the input end 2 of the reduction mechanism.
[0054] Planetary gear reduction mechanism, including:
[0055] The output terminal 1 of the reduction mechanism is used to output the power of the planetary gear reduction mechanism;
[0056] The input end 2 of the reduction mechanism is used to drive the action of the planetary gear reduction mechanism;
[0057] The planetary gear sets 3 are three sets, and the adjacent two sets of the planetary gear sets 3 are detachably connected. The planetary gear set 3 is respectively connected in transmission with the input end 2 of the reduction mechanism and the output end 1 of the reduction mechanism, and the output end 1 of the reduction mechanism is connected in transmission with the planet carrier 4 of the planetary gear set 3 ...
Embodiment 2
[0070] The difference between this embodiment and Embodiment 1 is that this embodiment provides a steering gear, a planetary gear reduction mechanism and a motor 12 , and the motor 12 is connected to the input end 2 of the reduction mechanism through transmission.
[0071] Planetary gear reduction mechanism, including:
[0072] The output terminal 1 of the reduction mechanism is used to output the power of the planetary gear reduction mechanism;
[0073] The input end 2 of the reduction mechanism is used to drive the action of the planetary gear reduction mechanism;
[0074] The planetary gear set 3 is a set, and the planetary gear set 3 is connected to the input end 2 of the reduction mechanism and the output end 1 of the reduction mechanism respectively, and the output end 1 of the reduction mechanism is connected to the planetary gear set 3 One of the planet carrier 4 and the outer ring gear 5 is connected in transmission;
[0075] The wiring sleeve 6 is arranged through ...
Embodiment 3
[0077] The difference between this embodiment and Embodiment 1 is that this embodiment provides a steering gear, a planetary gear reduction mechanism and a motor 12 , and the motor 12 is connected to the input end 2 of the reduction mechanism through transmission.
[0078] Planetary gear reduction mechanism, such as figure 1 with figure 2 shown, which includes:
[0079] The output terminal 1 of the reduction mechanism is used to output the power of the planetary gear reduction mechanism;
[0080]The input end 2 of the reduction mechanism is used to drive the action of the planetary gear reduction mechanism;
[0081] The planetary gear sets 3 are two groups, and the adjacent two groups of the planetary gear sets 3 are detachably connected. The planetary gear set 3 is respectively connected in transmission with the input end 2 of the reduction mechanism and the output end 1 of the reduction mechanism, and the output end 1 of the reduction mechanism is connected in transmissi...
PUM
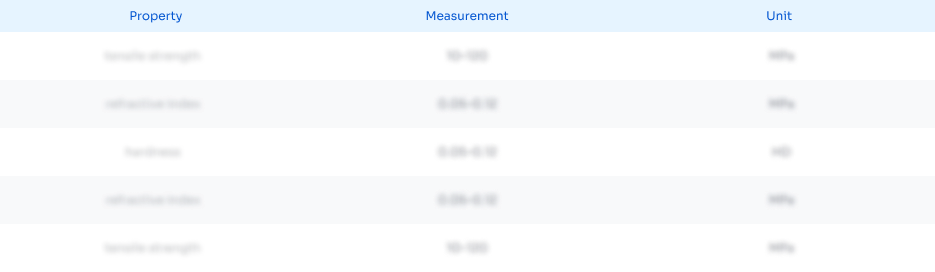
Abstract
Description
Claims
Application Information

- Generate Ideas
- Intellectual Property
- Life Sciences
- Materials
- Tech Scout
- Unparalleled Data Quality
- Higher Quality Content
- 60% Fewer Hallucinations
Browse by: Latest US Patents, China's latest patents, Technical Efficacy Thesaurus, Application Domain, Technology Topic, Popular Technical Reports.
© 2025 PatSnap. All rights reserved.Legal|Privacy policy|Modern Slavery Act Transparency Statement|Sitemap|About US| Contact US: help@patsnap.com