Tunnel corrugated steel plate reinforcing device and method
A technology of corrugated steel plates and reinforcement devices, which is applied in tunnels, tunnel linings, shaft equipment, etc., can solve problems such as safety risks, construction, and insufficient thickness of linings, solve disturbances and load increases, improve overall force-bearing capacity, and improve waterproofing performance effect
- Summary
- Abstract
- Description
- Claims
- Application Information
AI Technical Summary
Problems solved by technology
Method used
Image
Examples
Embodiment 1
[0049] This embodiment provides a tunnel corrugated steel plate reinforcement device, which includes a protective fixing frame 2 and a corrugated steel plate 3;
[0050] In use, the protective fixing frame 2 is attached to the inner wall surface of the tunnel lining 1, the gap between the protective fixing frame 2 and the inner wall surface of the tunnel lining is less than or equal to 15 cm, and the lower end of the protective fixing frame 2 passes through the arch. The foot structure is fixed on the inner wall surface of the tunnel.
[0051] Preferably, the protection fixing frame 2 is a T-shaped protection fixing frame, an H-shaped protection fixing frame, or a combination of a T-shaped protection fixing frame and an H-shaped protection fixing frame. The T-shaped protection fixing frame or the H-shaped protection fixing frame Use carbon steel Q235 or Q345 material, or other high-strength materials, such as high-strength aluminum alloys, carbon fiber materials, etc.
[0052...
Embodiment 2
[0070] This embodiment provides a tunnel corrugated steel plate reinforcement method, which can utilize the tunnel corrugated steel plate reinforcement device in Embodiment 1, including:
[0071] S10. Treatment of inner wall surface of lining concrete
[0072] Use an electric or pneumatic chisel to chisel the inner wall of the lining concrete, clean up the loose concrete and the floating ash on the inner wall, and use it to increase the bonding strength of the grouting in the later stage.
[0073] S20. Install the protective reinforcement frame
[0074] In this embodiment, the protection reinforcement frame is a T-type protection reinforcement frame or an H-type protection reinforcement frame, and the T-type protection reinforcement frame or the H-type protection reinforcement frame is made of carbon steel Q235 or Q345 material, or other high-strength materials. For example, high-strength aluminum alloys, carbon fiber materials, etc.
[0075] refer to figure 1 , the T-shape...
PUM
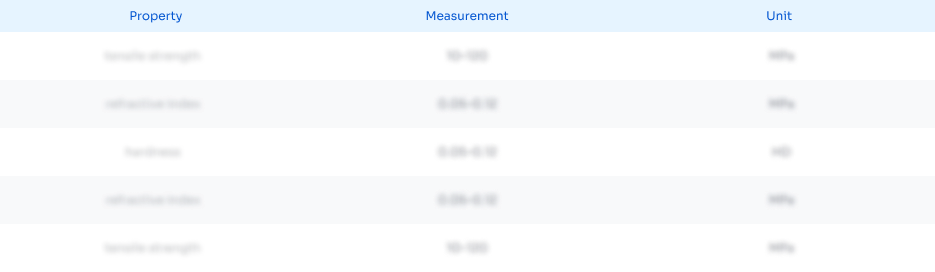
Abstract
Description
Claims
Application Information

- R&D
- Intellectual Property
- Life Sciences
- Materials
- Tech Scout
- Unparalleled Data Quality
- Higher Quality Content
- 60% Fewer Hallucinations
Browse by: Latest US Patents, China's latest patents, Technical Efficacy Thesaurus, Application Domain, Technology Topic, Popular Technical Reports.
© 2025 PatSnap. All rights reserved.Legal|Privacy policy|Modern Slavery Act Transparency Statement|Sitemap|About US| Contact US: help@patsnap.com