Environment-friendly polyester dyeing repair agent and preparation method thereof
An environmentally friendly polyester and repairing agent technology, which is applied in the dyeing and finishing field of the textile industry, can solve the problems of unrepairable color spots of polyester fibers, difficulty in achieving uniform dyeing, and affecting the economic benefits of enterprises, so as to achieve good product quality stability and environmental protection , Improve the effect of leveling effect
- Summary
- Abstract
- Description
- Claims
- Application Information
AI Technical Summary
Problems solved by technology
Method used
Examples
Embodiment 1
[0020] The present embodiment 1 is composed of the following raw material weight percentages: benzyl alcohol 25%, propyl benzoate 15%, benzyl alcohol polyoxyethylene ether 16%, fatty alcohol polyoxyethylene ether 15%, Tween-80 # 7%, tristyrene phenol polyoxyethylene ether 12%, solvent ethylene glycol 7%, high-efficiency defoamer 3%.
[0021] The specific operation steps are as follows:
[0022] (1) Add benzyl alcohol, propyl benzoate, benzyl alcohol polyoxyethylene ether, fatty alcohol polyoxyethylene ether, and Tween into the reaction kettle in turn to mix, and turn on the mixer to stir evenly.
[0023] (2) After stirring evenly for 30 minutes, add high-efficiency defoamer and tristyrene phenol polyoxyethylene ether respectively, and start to heat slowly at the same time. The temperature is controlled at 65°C, and the mixing reaction time is controlled at 2.5 hours.
[0024] (3) After the mixing reaction time is over, turn on the vacuum system and continue to stir evenly for...
Embodiment 2
[0029] The present embodiment 2 is composed of the following raw material weight percentages: benzyl alcohol 23%, propyl benzoate 16%, benzyl alcohol polyoxyethylene ether 17%, fatty alcohol polyoxyethylene ether 18%, Tween-80 # 6%, tristyrene phenol polyoxyethylene ether 11%, solvent propylene glycol 7%, high-efficiency defoamer 2%.
[0030] The specific operation steps are as follows:
[0031] (1) Add benzyl alcohol, propyl benzoate, benzyl alcohol polyoxyethylene ether, fatty alcohol polyoxyethylene ether, and Tween into the reaction kettle in turn for mixing, and turn on the mixer to stir evenly.
[0032] (2) After stirring evenly for 30 minutes, add high-efficiency defoamer and tristyrene phenol polyoxyethylene ether respectively, and start to heat slowly at the same time. The temperature is controlled at 70°C, and the mixing reaction time is controlled at 2 hours.
[0033] (3) When the mixing reaction time is over, turn on the vacuum system and continue to stir evenly f...
Embodiment 3
[0038] The present embodiment 3 is composed of the following raw material weight percentages: benzyl alcohol 23%, propyl benzoate 16%, benzyl alcohol polyoxyethylene ether 17%, fatty alcohol polyoxyethylene ether 18%, Tween-80 # 6%, tristyrene phenol polyoxyethylene ether 11%, solvent ethylene glycol 7%, high-efficiency defoamer 2%.
[0039] The specific operation steps are as follows:
[0040] (1) Add benzyl alcohol, propyl benzoate, benzyl alcohol polyoxyethylene ether, fatty alcohol polyoxyethylene ether, and Tween into the reaction kettle in turn to mix, and turn on the mixer to stir evenly.
[0041] (2) After stirring evenly for 30 minutes, add high-efficiency defoamer and tristyrene phenol polyoxyethylene ether respectively, and start to heat slowly at the same time. The temperature is controlled at 75°C, and the mixing reaction time is controlled at 3 hours.
[0042] (3) When the mixing reaction time is over, turn on the vacuum system and continue to stir evenly for 1 ...
PUM
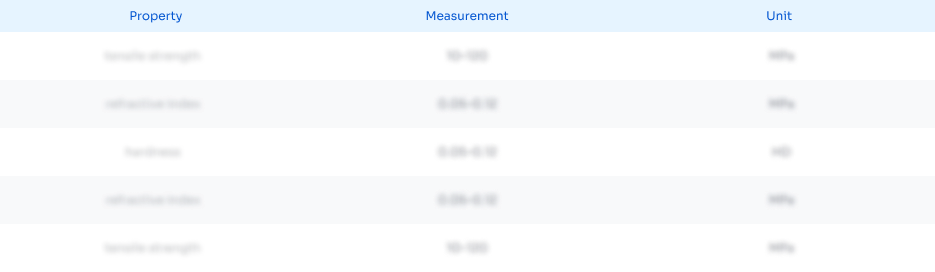
Abstract
Description
Claims
Application Information

- Generate Ideas
- Intellectual Property
- Life Sciences
- Materials
- Tech Scout
- Unparalleled Data Quality
- Higher Quality Content
- 60% Fewer Hallucinations
Browse by: Latest US Patents, China's latest patents, Technical Efficacy Thesaurus, Application Domain, Technology Topic, Popular Technical Reports.
© 2025 PatSnap. All rights reserved.Legal|Privacy policy|Modern Slavery Act Transparency Statement|Sitemap|About US| Contact US: help@patsnap.com