High-smoothness polishing rod for mechanical shaft
A high-finish, polished rod technology, applied in the direction of metal rolling, furnace type, furnace, etc., can solve the problem of high surface roughness of polished rods, and achieve the effect of reducing requirements, high smoothness and simplifying processing technology
- Summary
- Abstract
- Description
- Claims
- Application Information
AI Technical Summary
Problems solved by technology
Method used
Examples
Embodiment 1
[0033] A high-gloss polishing rod for mechanical shafts, comprising the following components: C: 0.180%, Si: 0.200%, Mn: 0.420%, P: 0.006%, S: 0.002%, Mo: 0.015%, Ni: 0.015 %, Cr: 0.040%, Cu: 0.020%, Sn: 0.010wt%, Sb: 0.010wt%, Cr: 10.5wt%, N: 0.010wt%, V: 0.250wt%, Ce: 0.800wt%, Co: 0wt%, Nb: 0.010wt%, B: 0.002wt%, Ti: 0.300%, the rest is Fe and impurity elements;
[0034] Casting: Melt the above raw materials into molten steel and continuously cast them into billets, heat the billets to 1100°C and forge them;
[0035] Rolled wire rod: A1: The steel billet after forging is subjected to four-roll rough rolling and finish rolling respectively, and the wire rod after finishing rolling is rolled and then hot-loaded off-line for heat treatment to ensure good and uniform cold working performance; each step in step A1 The elongation of the second rough rolling is 15%, and the elongation of each finish rolling is 5%.
[0036] A2: Put the rolled wire rod into the annealing furnace, ...
Embodiment 2
[0053] A high-gloss polishing rod for a mechanical shaft, comprising the following components: C: 0.220%, Si: 0.240%, Mn: 0.500%, P: 0.010%, S: 0.003%, Mo: 0.025%, Ni: 0.025 %, Cr: 0.060%, Cu: 0.035%, Sn: 0.150wt%, Sb: 0.015wt%, Cr: 13.0wt%, N: 0.020wt%, V: 0.800wt%, Ce: 1.300wt%, Co: 0.0300wt%, Nb: 0.080wt%, B: 0.004wt%, Ti: 0.800%, the rest is Fe and impurity elements;
[0054] Casting: Melt the above raw materials into molten steel and continuously cast them into billets, heat the billets to 1150°C and forge them;
[0055] Rolled wire rod: A1: The steel billet after forging is subjected to four-roll rough rolling and finish rolling respectively, and the wire rod after finishing rolling is rolled and then hot-loaded off-line for heat treatment to ensure good and uniform cold working performance; each step in step A1 The elongation of the second rough rolling is 20%, and the elongation of each finish rolling is 10%.
[0056] A2: Put the rolled wire rod into the annealing fu...
Embodiment 3
[0073] A high-gloss polishing rod for a mechanical shaft, comprising the following components: C: 0.200%, Si: 0.220%, Mn: 0.480%, P: 0.008%, S: 0.0025%, Mo: 0.020%, Ni: 0.020 %, Cr: 0.050%, Cu: 0.0275%, Sn: 0.0125wt%, Sb: 0.0125wt%, Cr: 11.5wt%, N: 0.015wt%, V: 0.520wt%, Ce: 1.05wt%, Co: 0.015wt%, Nb: 0.045wt%, B: 0.003wt%, Ti: 0.550%, the rest is Fe and impurity elements;
[0074] Casting: Melt the above raw materials into molten steel and continuously cast them into billets, heat the billets to 1125°C and forge them;
[0075] Rolled wire rod: A1: The steel billet after forging is subjected to four-roll rough rolling and finish rolling respectively, and the wire rod after finishing rolling is rolled and then hot-loaded off-line for heat treatment to ensure good and uniform cold working performance; each step in step A1 The elongation of the second rough rolling is 17%, and the elongation of each finish rolling is 8%.
[0076] A2: Put the rolled wire rod into the annealing f...
PUM
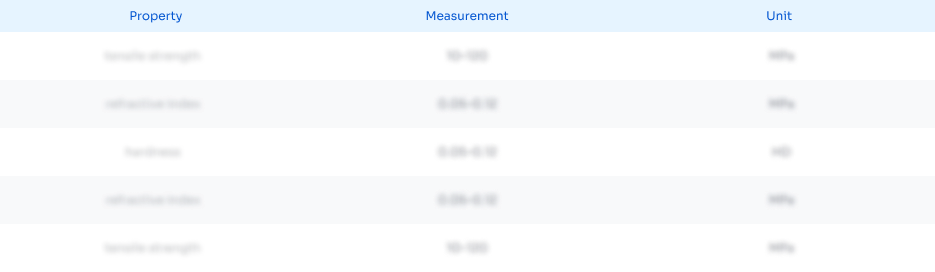
Abstract
Description
Claims
Application Information

- R&D
- Intellectual Property
- Life Sciences
- Materials
- Tech Scout
- Unparalleled Data Quality
- Higher Quality Content
- 60% Fewer Hallucinations
Browse by: Latest US Patents, China's latest patents, Technical Efficacy Thesaurus, Application Domain, Technology Topic, Popular Technical Reports.
© 2025 PatSnap. All rights reserved.Legal|Privacy policy|Modern Slavery Act Transparency Statement|Sitemap|About US| Contact US: help@patsnap.com