Reinforced glass fiber reinforced plastic and compression molding process thereof
A fiberglass and enhanced technology, applied in the field of glass fiber reinforced plastics, can solve the problems that a single fiberglass fiber reinforced plastic is difficult to meet complex and complex environmental requirements, and achieve the effects of maintaining durability and stability, enhancing plasticity, and improving durability
- Summary
- Abstract
- Description
- Claims
- Application Information
AI Technical Summary
Problems solved by technology
Method used
Image
Examples
Embodiment 1
[0053] A molding process of reinforced glass fiber reinforced plastic, characterized in that: comprising the following steps:
[0054] S1. Configuration: Heat and mix 30 parts of UP resin, 9.5 parts of PS synthetic glue, 66 parts of calcium carbonate powder, 1.5 parts of zinc stearate, and 1.8 parts of reinforcing agent to form a gel coat;
[0055]S2. Preparation: take one-tenth of the gel coat by mass, mix it with 3.3 parts of microporous foaming agent, impregnate it with 27 parts of glass fiber, dry it, and cut it into pieces to form a modulated fiber sheet;
[0056] S3. Molding: Clean the mold and heat it, then mix the remaining gel coat in the S1 configuration with 0.59 parts of TBPB tert-butyl ester, and then mix it with the modulated fiber sheet obtained in the S2 modulation, and inject it into the mold. keep warm for a period of time;
[0057] S4. Finished product: deflate the FRP, slowly cool it, and demold it to obtain a reinforced FRP.
[0058] The preparation proc...
Embodiment 2
[0067] A molding process of reinforced glass fiber reinforced plastic, characterized in that: comprising the following steps:
[0068] S1. Configuration: Heat and mix 25 parts of UP resin, 12 parts of PS synthetic glue, 60 parts of calcium carbonate powder, 2 parts of zinc stearate, and 1.5 parts of reinforcing agent to form a gel coat;
[0069] S2. Preparation: take 1 / 10 of the gel coat by mass, mix it with 4 parts of microporous foaming agent evenly, impregnate it with 18 parts of glass fiber, dry it, and cut it into pieces to form a modulated fiber piece;
[0070] S3. Molding: Clean the mold and heat it, then mix the remaining gel coat in the S1 configuration with 1 part of TBPB tert-butyl ester, and then mix it with the modulated fiber sheet obtained in the S2 modulation, inject it into the mold, and keep warm for a period of time;
[0071] S4. Finished product: deflate the FRP, slowly cool it, and demold it to obtain a reinforced FRP.
[0072] The preparation process of...
Embodiment 3
[0081] A molding process of reinforced glass fiber reinforced plastic, characterized in that: comprising the following steps:
[0082] S1. Configuration: Heat and mix 35 parts of UP resin, 8 parts of PS synthetic glue, 70 parts of calcium carbonate powder, 1 part of zinc stearate, and 2 parts of reinforcing agent to form a gel coat;
[0083] S2. Preparation: take one-tenth of the gel coat by mass, mix it with 2 parts of microporous foaming agent, and impregnate it with 30 parts of glass fiber, dry and cut it into pieces to form a modulated fiber sheet;
[0084] S3. Molding: clean the mold and heat it, then mix the remaining gel coat in the S1 configuration with 0.5 part of TBPB tert-butyl ester, and then mix it with the modulated fiber sheet obtained in the S2 modulation, inject it into the mold, and keep warm for a period of time;
[0085] S4. Finished product: deflate the FRP, slowly cool it, and demold it to obtain a reinforced FRP.
[0086] The preparation process of the...
PUM
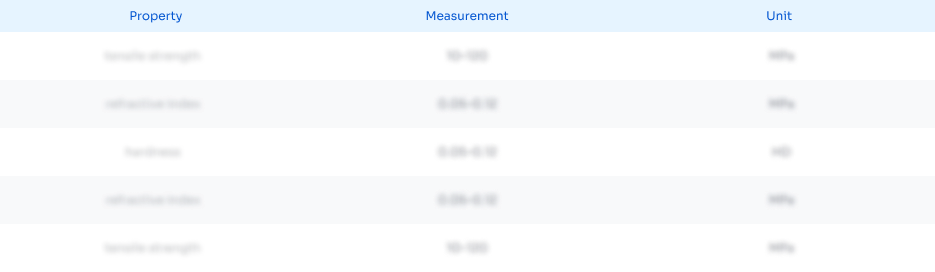
Abstract
Description
Claims
Application Information

- R&D Engineer
- R&D Manager
- IP Professional
- Industry Leading Data Capabilities
- Powerful AI technology
- Patent DNA Extraction
Browse by: Latest US Patents, China's latest patents, Technical Efficacy Thesaurus, Application Domain, Technology Topic, Popular Technical Reports.
© 2024 PatSnap. All rights reserved.Legal|Privacy policy|Modern Slavery Act Transparency Statement|Sitemap|About US| Contact US: help@patsnap.com