Anticorrosion and antifouling integrated self-repairing microcapsule and preparation method thereof
A technology of self-healing microcapsules and microcapsules, applied in the direction of microcapsule preparation, microsphere preparation, anti-corrosion coatings, etc., can solve the problems of low anti-biofouling performance, achieve enhanced anti-fouling performance, convenient test conditions, and prolong Effect of anti-corrosion and anti-fouling ability and anti-corrosion and anti-fouling life
- Summary
- Abstract
- Description
- Claims
- Application Information
AI Technical Summary
Problems solved by technology
Method used
Image
Examples
Embodiment 1
[0025] The anti-corrosion and anti-fouling integrated self-healing microcapsule preparation method involved in this example uses emulsion polymerization to prepare two-component microcapsules. The capsule core is tung oil (T) and non-toxic phenolic antifouling agent (F), and the capsule wall is urea-formaldehyde Resin, the specific process is: take 260mL of ultra-pure water, add 2g of emulsifier OP-10, use a stirring disperser to stir until completely dissolved, then add 5g of urea, 0.5g of ammonium chloride and 0.5g of resorcinol in sequence, dissolve Finally, adjust the pH value to 3.0 with a mass percentage concentration of 1% hydrochloric acid aqueous solution for acidification, then add 3g of T and F (the mass ratio of T and F is 5:1), stir and emulsify until the oil is completely emulsified , heated to 60°C, and 13.67g of formaldehyde solution was added dropwise. At a temperature of 60°C and a rotation speed of 800rpm / min, urea and formaldehyde underwent polycondensation ...
Embodiment 2
[0027] The anti-corrosion and anti-fouling integrated self-healing microcapsule preparation method involved in this example uses emulsion polymerization to prepare two-component microcapsules. The capsule core is tung oil (T) and non-toxic phenolic antifouling agent (F), and the capsule wall is urea-formaldehyde Resin, the specific process is: take 1000mL ultrapure water, add 8g of emulsifier OP-10, use a stirring disperser to stir until it is completely dissolved, then add 20g of urea, 2g of ammonium chloride and 2g of resorcinol in sequence, after dissolution, Adjust the pH value to 2.5 with a mass percent concentration of 1% hydrochloric acid aqueous solution for acidification, then add 20g of T and F (the mass ratio of T and F is 5:1), stir and emulsify until the oil is completely emulsified, heat To 60°C, add 50g of formaldehyde solution drop by drop, under the conditions of temperature of 60°C and rotation speed of 1000rpm / min, fully react for 2h, after the reaction is co...
Embodiment 3
[0029] The anti-corrosion and anti-fouling integrated self-healing microcapsule preparation method involved in this example uses the emulsion polymerization method to prepare two-component microcapsules. The capsule core is tung oil (T) and tin-free self-polishing antifouling paint (F), and the capsule wall is urea-formaldehyde resin. , the specific process is as follows: take 1000mL ultrapure water, add 10g emulsifier OP-10, stir until completely dissolved with a stirring disperser, then add 20g urea, 2g ammonium chloride and 2g resorcinol in sequence, after dissolving, use The mass percent concentration is 1% hydrochloric acid aqueous solution, adjust the pH value to 3.0 for acidification, then add 40g of T and F (the mass ratio of T and F is 4:1), stir and emulsify until the oil is completely emulsified, and heat to 60°C, add 50g of formaldehyde solution drop by drop, under the condition of temperature of 60°C and rotation speed of 1000rpm / min, fully react for 2h, after the ...
PUM
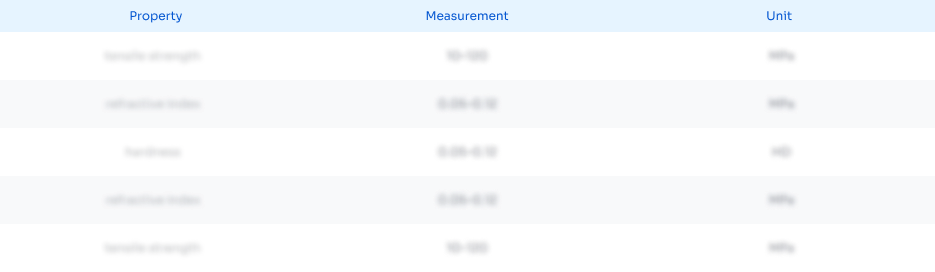
Abstract
Description
Claims
Application Information

- R&D
- Intellectual Property
- Life Sciences
- Materials
- Tech Scout
- Unparalleled Data Quality
- Higher Quality Content
- 60% Fewer Hallucinations
Browse by: Latest US Patents, China's latest patents, Technical Efficacy Thesaurus, Application Domain, Technology Topic, Popular Technical Reports.
© 2025 PatSnap. All rights reserved.Legal|Privacy policy|Modern Slavery Act Transparency Statement|Sitemap|About US| Contact US: help@patsnap.com