Plastic woven bag producing, manufacturing and processing system
A plastic woven bag and processing system technology, applied in flexible container manufacturing, paper making, bag making operations, etc., can solve the problems of superimposed deformation and increase in the number of plastic woven bags
- Summary
- Abstract
- Description
- Claims
- Application Information
AI Technical Summary
Problems solved by technology
Method used
Image
Examples
Embodiment Construction
[0026] The specific embodiment of the present invention will be described in further detail by describing the embodiments below with reference to the accompanying drawings, the purpose is to help those skilled in the art to have a more complete, accurate and in-depth understanding of the concept and technical solutions of the present invention, and To facilitate its practice, but not as a limitation of the invention.
[0027] See attached Figure 1-7 As shown, a plastic woven bag manufacturing and processing system includes a frame 1, a belt conveyor 2, a lateral pulling smoothing mechanism 3, a flexible guide roller 4, a leveling mechanism 5 and a winding mechanism 6, and the frame 1 It includes two supporting side frames 11, and the belt conveyor 2, leveling mechanism 5 and winding mechanism 6 are sequentially arranged between the two supporting side frames 11 according to the conveying direction of the belt conveyor 2;
[0028] Two flexible guide rollers 4 are arranged bet...
PUM
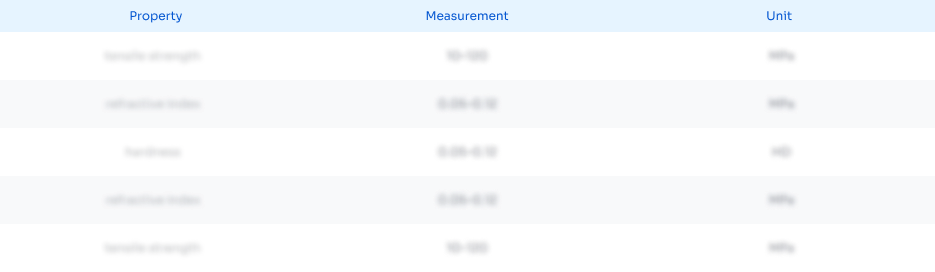
Abstract
Description
Claims
Application Information

- R&D
- Intellectual Property
- Life Sciences
- Materials
- Tech Scout
- Unparalleled Data Quality
- Higher Quality Content
- 60% Fewer Hallucinations
Browse by: Latest US Patents, China's latest patents, Technical Efficacy Thesaurus, Application Domain, Technology Topic, Popular Technical Reports.
© 2025 PatSnap. All rights reserved.Legal|Privacy policy|Modern Slavery Act Transparency Statement|Sitemap|About US| Contact US: help@patsnap.com